External cylindrical grinding - optimum cooling
External cylindrical grinding is one of the most frequently used grinding processes on CNC machine tools in industrial applications. This process is frequently used for hard-fine machining of cylindrical outer surfaces, as it is the most suitable process for machining rounded surfaces (e.g. cylindrical surface) on the outside of a mostly rotationally symmetrical component.
In external cylindrical grinding, a grinding wheel is used as a tool, which is then brought into contact with the workpiece surface and thus ensures the desired surface finish. From extremely small and delicate components, e.g. for injection nozzles, to large shafts, components with high surface requirements are externally cylindrical ground.
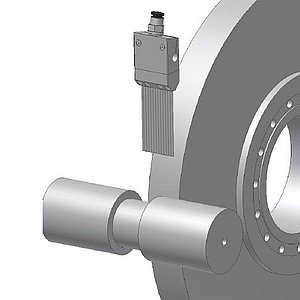
Classification of external cylindrical grinding processes
External cylindrical grinding can be further categorized according to two characteristics. On the one hand, external cylindrical grinding is categorized according to the positioning of the component during machining, and on the other hand according to the main feed direction.
Storage of the component
Component storage during machining: Intermediate point grinding During intermediate point grinding, the component is rotatably supported at the end faces in a clamping device in the machine tool. For this purpose, a centric depression must first be made in the workpiece on the end faces in a preceding machining step in order to ensure secure fixing. After clamping, the component is machined on one side by the rotating grinding wheel. Centerless grinding
Main feed direction
Main feed direction during component machining External cylindrical circumferential cross grinding In this form of external cylindrical grinding, the main feed direction is transverse to the circumferential direction. This leads to a reduction in the cross-section of the component in the width of the grinding wheel, which removes material in the direction of the axis of rotation. External circumferential longitudinal grinding The kinematics for external circumferential longitudinal grinding are the opposite, with the grinding wheel moving parallel to the axis of rotation of the component. Challenges in external cylindrical grinding
Parameters for external cylindrical grinding
As with all grinding processes, external cylindrical grinding must also be set using many parameters. The aim is to achieve a short cycle time, consistent machining quality and burn-free machining. From the point of view of cooling lubricant supply, there are two main targets for external cylindrical grinding:
Sufficient supply of cooling lubricant: During external cylindrical grinding, the process heat generated by friction and shear work must be dissipated by the cooling lubricant to prevent thermal overstressing of the component. To achieve this, sufficient cooling lubricant must be introduced into the grinding gap at a suitable speed. The speed plays an important role because if the speed is too low, the cooling lubricant cannot penetrate the air cushion rotating with the grinding wheel and therefore cannot reach the machining zone.
Avoiding chatter marks: The interaction between the tool and workpiece contact and the cooling lubricant is problematic during external cylindrical grinding. An excessive supply of cooling lubricant can lead to effects similar to “aquaplaning”, in which the tool's engagement with the workpiece is temporarily lost. This process induced by cooling lubricant is referred to in manufacturing technology as “coolant chatter”, which can also be detected acoustically on the machine tool. The “coolant chatter” affects the roundness of the component. Depending on the severity, clear roundness errors can be seen on a corresponding measurement chart. Optimum cooling lubricant supply during external cylindrical grinding
Challenges in external cylindrical grinding
An optimum cooling lubricant supply is just as important in external cylindrical grinding as in other grinding processes and brings with it a number of challenges::
- If necessary, small installation spaces for nozzle positioning.
- Cooling lubricant discharge speed as required.
- Targeted lubricoolant feed into the machining zone.
- Difficult feed conditions for the cooling lubricant due to limited installation space for nozzles and feeds.
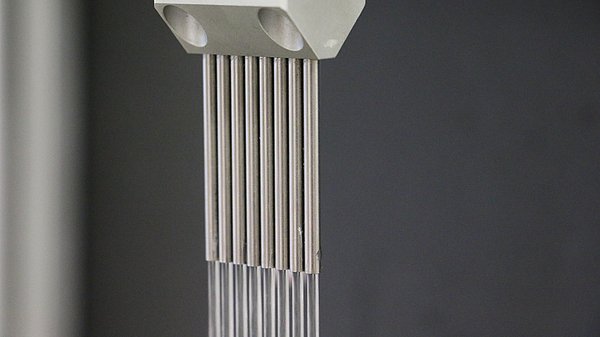
Note when cooling the external cylindrical grinding
A number of factors must be taken into account for the optimum supply of cooling lubricant, which can have a very positive effect on the machining result. For optimum cooling during external cylindrical grinding, the following must be observed:
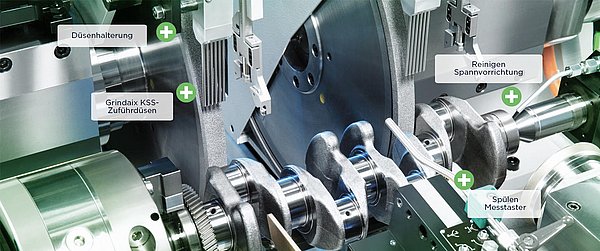
The selection of a suitable nozzle is essential for an adequate lubricoolant supply. The cooling lubricant nozzle should completely supply the component contour of the grinding wheel engagement volume to be machined with cooling lubricant so that the chip formation process is sufficiently lubricated and cooled. Cooling lubricant nozzles that are adapted to the component or grinding wheel geometry are ideal. This may be necessary if the component has several steps (e.g. gear shafts). Sufficient installation space must be available within the machine for the intended nozzle.
In addition to targeted supply, the cooling lubricant nozzle also ensures that the cooling lubricant exits the nozzle at a sufficiently high speed. The exit speed depends on the pressure and volume flow provided in the supply to the nozzle. The exit speed from the cooling lubricant nozzle depends on the peripheral speed of the grinding wheel. Both values must be adapted to each other accordingly. If both parameters are aligned with each other, the cooling lubricant jet “sticks” to the grinding wheel and is optimally applied to the processing zone.
To ensure that the nozzle can guarantee a targeted coolant supply, it is essential that the nozzle is precisely aligned with the grinding gap. Various aids can be used for this, such as the coolant pointer, which marks the exact point of impact with a laser beam. If the nozzle is not aligned correctly, an adequate coolant supply in the grinding gap cannot be guaranteed, even if all the other process supply parameters are adhered to.
Cleaning the grinding wheel: The coolant supply can have a significant positive influence on the cleanliness of the grinding wheel through special cleaning nozzles. Cleaning nozzles use coolant to flush machining residues out of the pores of the grinding wheel, which would otherwise have reduced the cutting ability of the grinding tool. The necessity of using a cleaning nozzle also depends heavily on the material to be machined, the grinding wheel specification (pore space) and the process parameters.
Advantages of optimal cooling
Many aspects must be considered when supplying cooling lubricant. It is not uncommon for an optimal cooling lubricant supply to be complex and for the cooling lubricant supply systems supplied by the machine manufacturer to be inadequate. Nevertheless, the cooling lubricant supply is a key factor influencing the machining result, and can have a very positive or very negative impact. The advantages of performing a manufacturing task with an optimized coolant supply can be summarized as follows:
An optimized cooling lubricant supply can achieve a higher feed rate and thus a higher cutting performance with process reliability. This results in a reduction in cycle times and thus increased productivity of the machine tool.
The surface requirements for the ground surfaces can be better met due to the chip formation processes being sufficiently supplied with coolant. Grinding burn is avoided and the cutting depth is also close to the theoretically calculated size, which is deliberately selected by machine tools. Thus, the machine tool produces reliably in consistent quality.
The targeted supply of the cooling lubricant eliminates the need for flood cooling with high cooling lubricant volume flows. In addition to the increased efficiency, the cooling lubricant-related overheads that arise from the purchase, supply, temperature control and filtration of the cooling lubricant are also reduced.
The thermal relief and reliable cleaning of the grinding wheel from clogging extends its service life. The abrasive itself, but also the bond of the grinding wheel, are subjected to less stress, which has a positive effect on the service life. The grinding wheel remains cuttable for much longer due to the use of cleaning nozzles, which makes dressing the grinding wheel much less necessary.
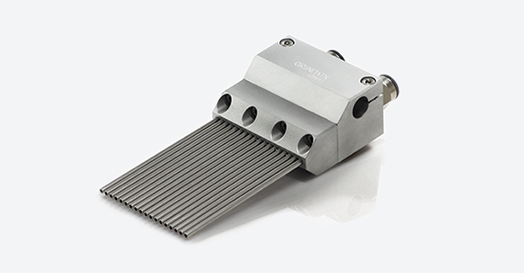
Summary
Cylindrical grinding is a frequently used manufacturing process and is used to machine round external surfaces of workpieces. As with all other grinding processes, effective cooling lubricant supply is also important for cylindrical grinding. The cooling lubricant supply must be determined and adjusted based on various parameters. With an optimal design, the cooling lubricant supply has a very positive effect on the machining task in terms of quality, cost-effectiveness and reliability.
Products relevant to this article:
You may also be interested in these articles from our magazine:
Frequent problems during grinding
Although grinding is a widely used manufacturing process, it is nevertheless complex and carries the risk of making mistakes in many places. In all cases, these have an impact on efficiency and component quality. Read on to find out what needs to be taken into account in detail and what the most common errors in grinding actually are.
Grinding burn
Thermal edge zone damage due to structural changes - commonly known as grinding burn. We explain the material-technical background and provide initial approaches for preventing grinding burn.
Cooling lubricant supply
It is easy to understand that grinding processes need to be supplied with cooling lubricant. But what exactly does the cooling lubricant do and what are the challenges involved in supplying cooling lubricant?
Coolant filtration systems
Treatment is a crucial part of the cooling lubricant supply with a major impact on production results and efficiency. We have described and compared the usual filtration processes for cooling lubricants.