Printing components (3D)
The manufacturing processes that are summarized under the term 3D printing have been on everyone's lips for some time now and are undergoing rapid technical development. Due to the ever more cost-efficient and also more powerful process options with shorter processing times and increasing quality of the printed components, 3D printing processes are becoming increasingly attractive for both industrial and private applications.
3D printing processes differ considerably from conventional manufacturing processes, even from a purely conceptual point of view. While machining processes (e.g. turning, milling, drilling) are subtractive manufacturing processes, 3D printing is an additive manufacturing process. Subtractive manufacturing processes remove material from a semi-finished product until the desired shapes and dimensions are achieved. Additive processes produce the component directly in the desired dimensions so that no semi-finished product is required or material has to be removed.
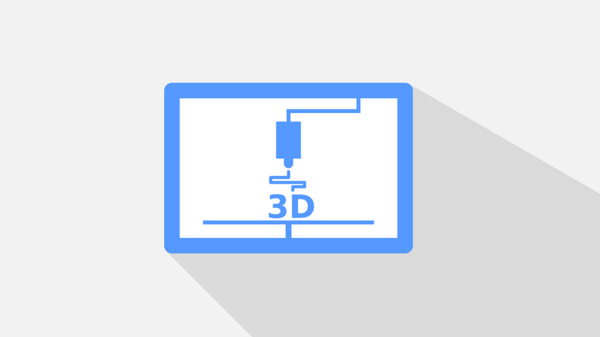
3D printing with a wide range of materials and processes
3D printing is already possible today with a wide variety of materials. Initially, it was common to use plastics, which can now also be implemented for private use with relatively inexpensive 3D printers. The 3D printing of metal components using a laser-sintering process is used more industrially. The costs of laser sintering are considerably higher, but the components can withstand much greater stresses.
Fused Deposition Modeling (FDM)
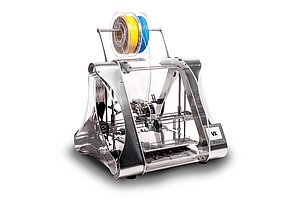
Fused deposition modeling (FDM) is commonly used for 3D printing with plastic materials. In this process, a suitable plastic is first liquefied by heat and then applied in layers to a carrier plate using a print head. The applied plastic undergoes a rapid increase in viscosity and becomes solid so that the next layer can be applied. In this way, the component is built up layer by layer from bottom to top.
Laser sintering
Unlike the FDM process, 3D laser sintering does not emit a liquefied material from a print head. Instead, a powder of the desired material is melted by a laser beam. Starting from a metal carrier plate, thin layers of powder are “welded” together one after the other, similar to classic build-up welding, so that the desired component is also printed layer by layer in laser sintering. Some metals and metal alloys are suitable for laser sintering, including titanium and stainless steel, for example. However, other alloys are unfortunately unsuitable for technical reasons and current possibilities.

Special features of laser sintering:
+ Production of metallic components
+ Layer thickness between 20-60 µm
+ Several components can be printed in one operation
- Post-processing of the surface required
- Powder must be removed after printing
- Not all metal alloys can be printed
Possibilities of 3D printing
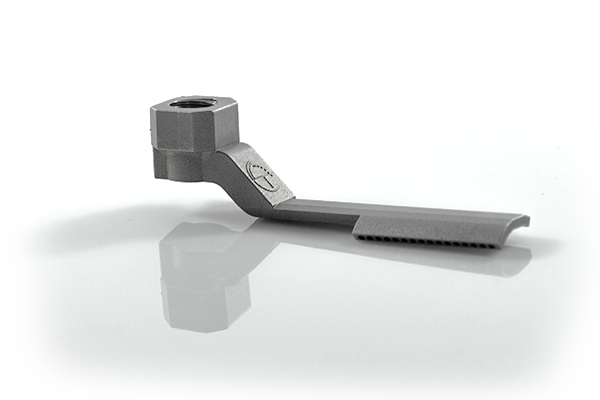
Component designs cannot be designed arbitrarily, as they must also be producible with the available manufacturing method. Particularly in the case of machining production processes, special attention must be paid to these production requirements in order to keep production costs as low as possible. 3D printing significantly increases geometric flexibility. Contours, undercuts or cavities that were previously impossible to produce can now be realized using 3D printing without the usual manufacturing restrictions. The very high geometric flexibility associated with this new process also makes it possible to produce components that are considerably lighter in some cases, which offers great potential for optimization, e.g. for components used in aircraft. With 3D printed components, the geometry follows the subsequent function, not the other way around. This means that 3D printed components can be adapted much better to their later use than was previously the case with production-ready components. However, completely new approaches are required for the planning and design of additively manufactured components.
Special features of 3D printing and challenges in manufacturing
Certain geometries, especially curves and fillets, have a process-related disadvantage in 3D printing. These must be provided with supports so that the desired geometry can be achieved. The support structure must be removed again once the component has been completed, which requires an additional post-processing step. If the support structure is located in places that are difficult to access, e.g. in cavities, the removal of this support structure can be very time-consuming or even impossible. The need for support structures can be avoided from a design point of view, but this makes it necessary to take these 3D printing-specific requirements for support load-compliant design into account when designing the component.
Due to the layered structure of the component during 3D printing, the process results in a step-like structure of the component. This means that the surface quality of additively manufactured components is many times worse than that of conventionally manufactured workpieces. Layer thicknesses vary between 20-60µm and more and therefore determine the edge fracture structure of the additively generated surface.
In almost all cases, post-processing is also required for holes, threads and fits. Furthermore, the heat introduced to melt the material can lead to heat distortion in the component, which has a negative impact on the dimensional accuracy of the 3D printed component.
The metal powder used also poses a safety risk. In addition to the highly harmful effect of inhaling the respirable fine particles, contact of the dust with open fire can lead to a dust explosion. Thorough removal of the metal powder is therefore necessary, also to prevent excessive discharge of the still usable powder from the machine for purely economic reasons.
As the laser sintering process causes a great deal of heat to enter the component, the material becomes brittle. This is accompanied by a loss of toughness, which means that 3D printed components have disadvantages compared to conventionally manufactured components for certain load spectra.

Additive versus subtractive manufacturing: Advantages and disadvantages
Below we have compared and contrasted the most important features of conventional and subtractive manufacturing and 3D printing in a table. In principle, a precise examination of the advantages and disadvantages as well as a coordinated design is always required in order to fully utilize the advantages of 3D printing.
Fulfills the requirements in comparison: ++ much better; +better; o similar; - worse; -- much worse
Property
Processing time |
Post-processing |
Surface quality |
Material consumption |
Energy consumption |
Design effort |
Freedom of geometry |
production costs |
Subtractive manufacturing
+ |
+ |
+ |
- - |
+ |
+ |
- |
+ |
Additive manufacturing
- - |
- |
- - |
+ + |
- |
- |
+ + |
- - |
Summary
3D printing is still in the development stage, but is gradually and increasingly establishing itself in industrial, professional applications. In addition to some disadvantages and necessary reworking of 3D printed components, 3D printing offers completely new flexibility in the design and manufacture of components. Grindaix GmbH has also taken advantage of this to design cooling lubricant nozzles that are much more function-oriented. The form follows the function, manufacturing restrictions are reduced and better, tailor-made components can be realized.
Would you like to equip your machine tool with flow- and application-optimized coolant nozzles? We are your partner - because we combine our expertise in the field of lubricoolant supply in machine tools with professional flow simulation to achieve an optimum, application-oriented design for your cooling lubricant nozzles. During production, we cooperate with experienced 3D printing companies in the field of laser sintering. You can find some examples of our 3D printed nozzles here. If you are interested in an optimized (possibly 3D-printed) coolant nozzle, simply get in touch with us! We look forward to your inquiry.
Products relevant to this article:
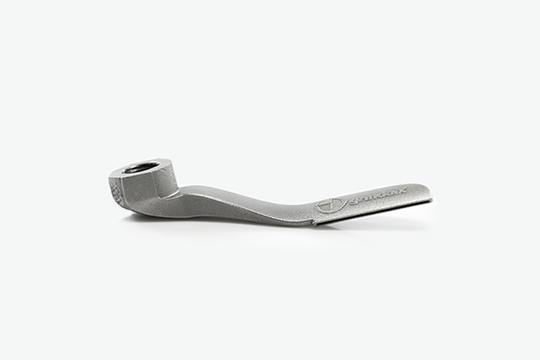
You may also be interested in these articles from our magazine:
Frequent problems during grinding
Although grinding is a widely used manufacturing process, it is nevertheless complex and carries the risk of making mistakes in many places. In all cases, these have an impact on efficiency and component quality. Read on to find out what needs to be taken into account in detail and what the most common errors in grinding actually are.
Grinding burn
Thermal edge zone damage due to structural changes - commonly known as grinding burn. We explain the material-technical background and provide initial approaches for preventing grinding burn.
Cooling lubricant supply
It is easy to understand that grinding processes need to be supplied with cooling lubricant. But what exactly does the cooling lubricant do and what are the challenges involved in supplying cooling lubricant?
Coolant filtration systems
Treatment is a crucial part of the cooling lubricant supply with a major impact on production results and efficiency. We have described and compared the usual filtration processes for cooling lubricants.