Cooling lubricant and its relevance in grinding processes
In machining processes, it is part of the process to use cooling lubricants so that the process can be carried out without any problems.
For example, in grinding in particular, great importance is attached to the use of cooling lubricant so that grinding burn can be prevented and the quality of the workpiece can be guaranteed. In the following magazine article, this topic will be explained in more detail and thegrinding process will be dealt with, focusing here on the relevance of the cooling lubricant.
The grinding process - an ablative process
Grinding is a metal-cutting manufacturing process for fine and finish machining of workpieces, which is characterized primarily by the fact that the contact area between the workpiece and the tool is relatively large. In the manufacturing process, the tool rotates while the workpiece performs either rotational or translational movements. In this process, a large number of small cutting edges at a high cutting speed ensure that the material is removed. Only a small amount of material is removed per cutting edge, which results in a low load on the individual cutting edges. This enables high shape and dimensional accuracy during machining. But the surface finish is also characterized by high quality. This is why this machining process is traditionally used in finishing, as it gives the finished workpiece the smooth surface that cannot usually be achieved by other manufacturing processes such as milling or turning. Therefore, one of the reasons why grinding is predominantly used is the high demands on the workpiece and the enormous importance of the surface quality. The desired surface quality is achieved by using high hardness grinding grits such as CBN, etc. These increasing demands on the part being produced contrast with the reductions in cycle time of grinding machines.
During grinding, excess material is removed in the form of chips and a fine burr is set up. These chips are the waste product produced in the process and are referred to as "grinding dust" or "grinding sludge". Accordingly, grinding is the separation of material layers in the form of chips by randomly shaped abrasive grains that do not have a defined angle. In this process, the material is compressed in front of the grain cutting edge during the chip formation process and, depending on the engagement position of the cutting edge, is displaced forwards or sideways. When the material shear stress is exceeded, a chip is cut off.
For this reason, grinding, like the honing manufacturing process, is assigned to the subgroup "Machining with geometrically indeterminate cutting edge". Above all, however, grinding stands out from the other manufacturing processes due to its high accuracy and precision.
Why is cooling lubricant important?
During grinding, the shearing, cutting and friction processes generate a large amount of heat, only a small part of which is dissipated with the chips produced. As a result, considerable thermal stress is exerted on the tool and workpiece. This burden during machining can lead to an undesirable change in the microstructural properties in the near-surface edge zone (e.g. grinding burn). The solution to this problem: cooling lubricant (KSS for short).
Various types of coolant are available. These can be roughly divided into: non-water-miscible KSS and the water-miscible KSS concentrate.
But also the tasks that KSS has in the grinding process can be divided into two groups, the primary and secondary tasks. The primary tasks of KSS is to reduce the friction between the abrasive grain and the workpiece and between the bond and the workpiece by forming a stable lubricating film. Furthermore, the contact zone and the workpiece surface are cooled by the absorption and transport of heat. The secondary tasks of KSS are the cleaning of the grinding wheel and the workpiece. Also the removal of chips from the machining zone. The last task is the formation of a corrosion protection for the machine and the workpiece material.
This cooling with coolant ensures that thermal damage to the component and tool is reduced, for example to prevent grinding burn. There is a kind of interaction between the lubricating and cooling functions of cooling lubricant. The lubricating effect is influenced by the type of cooling lubricant used and by the composition of the MWF.
Cooling lubricant in the grinding process
All components involved in the grinding process are subject to strong mechanical, chemical or thermal stress. The use of cooling lubricant can reduce or even eliminate these disturbances. With the use of coolant, the friction between the workpiece to be produced and the tool is reduced, the heat is dissipated and the chips are flushed out of the machining zone. Thus, in addition to reducing the friction between the workpiece and the tool, the wear phenomenon is also reduced, which is ultimately reflected in a higher quality of the workpieces. This is because the dimensional and form accuracy, as well as the surface quality and the edge zone properties, can be positively influenced by the added coolant. This coolant supply ensures a smooth process and reduces the probability of grinding burn.
Finally, the condition for a grinding process free of grinding burn is the sufficient supply of the machining zone by the cooling lubricant. Furthermore, there are other influencing parameters that are essential for a successful grinding process. These include the inhomogeneity of the tool quality, the constantly changing dressing ratios and geometries due to wear. But also the variance in process control, the use of coolant lubricants and the use of outdated cooling lubricant supply systems. These individual factors can affect the quality of the grinded workpiece. However, the supply of cooling lubricant is more difficult because the contact area between the part and the grinding tool is larger. Therefore, sufficient coolant supply in the machining zone is of greater relevance. The cooling lubricant influences the chip formation process by forming a lubricating film and ensures a reduction of the frictional forces, as well as cooling of the material and tool surface. By suppressing the frictional forces, the resulting frictional heat in the process is reduced. Consequently, the heat generated in the process is minimized as a result. Furthermore, this reduction in friction also manifests itself through the chip flow line.
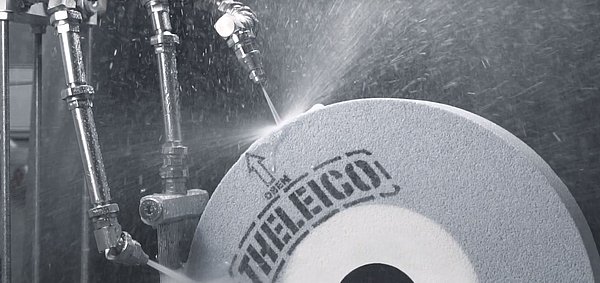
By reducing the friction between the grain cutting edge, the grinding wheel bond and the chip, this results in a reduction of abrasion on the bond material and thus the development of grinding wheel wear is significantly reduced. Another factor that makes it difficult to feed coolant into the contact zone is the air cushion that forms around the grinding wheel. Due to the rotating grinding wheel, the ambient air is sucked in laterally and discharged again via the outer surfaces in a radial direction. These flow forces created by the air cushion ensure that the cooling lubricant is diverted and thus does not reach the contact zone between the grinding wheel and the workpiece. This results in an undersupply of coolant and the risk of grinding burn increases. This can only be prevented by effective cooling lubrication, in which the coolant jet applies a certain speed to overcome the air cushion. Another possibility is to divert the air cushion. This is possible both mechanically, by means of so-called deflector plates, and by means of a high-pressure liquid jet.
The correct use of cooling lubricant during grinding
As mentioned at the beginning, thermal overload of the workpiece edge zone and also wear of the grinding wheel are a major problem in the machining production process. It is not the high quantity of cooling lubricant used in the machining process that is decisive, but how much of the coolant used reaches the actual machining zone. Accordingly, attention should be paid to the sufficient and appropriate amount of cooling lubricant for the grinding process. If there is an undersupply of coolant, this will ensure that the process heat is not sufficiently removed. On the other hand, an oversupply of coolant is just as destructive as an undersupply. Excessive lubrication can have negative effects, as it can prevent the cutting process and comparatively more energy is required for shear and quantity of cooling lubricant for material removal to take place. However, above a certain volume flow of cooling lubricant, a kind of saturation of the pore space takes place. This leads to the fact that no more cooling lubricant can enter the contact zone. Too much coolant can also lead to "aquaplaning effects" and vibrations in the grinding process. Nevertheless, even this proportion of coolant that does not enter the machining zone can have a positive effect on the grinding result.
The heat on the workpiece no longer accumulates and the machine room is cooled. Furthermore, it is possible that this can also have a negative effect on process costs and significantly increase the environmental impact.
Likewise, the power requirement of the spindle drive increases as the cooling lubricant volume flow increases, since the cooling lubricant transported by the grinding wheel must be accelerated to the peripheral speed of the grinding machine. The greater the speed difference between the jet and the wheel, the greater the power required. And it is precisely this increased cutting speed that makes cooling of the contact zone more difficult.
Minimum quantity lubrication
Minimum quantity lubrication (MQL) is a way of saving cooling lubricant in the machining process. The coolant is supplied in small quantities and thus contrasts with conventional coolant supply strategies, which are usually based on an oversupply of coolant. With minimum quantity lubrication, only a small amount of coolant is required. However, this can result in dry workpieces and dry chips.
The quantity of cooling lubricant used is reduced to the amount required for lubrication and cooling using a metering technique and brought under pressure, or with compressed air, directly to the point of engagement of the tool cutting edge. Empirically, the values of the cooling lubricant used for this purpose are between five and 50 ml per hour.
![[Translate to Englisch:] Grindaix - Schleifmaschine mit einer Grindaix Düse [Translate to Englisch:] Grindaix - Schleifmaschine mit einer Grindaix Düse](https://grindaix.de/fileadmin/Public/Bilder/Magazin/02_Schleifen/Schleifmaschine_2_ohne_Beschriftung.png)
The advantages of this are low lubricant consumption and the elimination of coolant filtration and recirculation. Furthermore, it is possible to enable a targeted supply of the cooling lubricant to and via the tool, as well as the elimination of biocides and fungicides. Of course, this optimization of the coolant supply also has its disadvantages, such as an increased thermal risk, which can end in a grinding burn. But the fact that MQL is a loss lubrication also puts this process in a negative light, as do the increased tool costs and the removal of machining residues, which then only have to be done by hand. The loss lubrication arises from the fact that in contrast to the circulation-based conventional wet machining, with the MQL the leaked lubricant cannot be reprocessed.
Above all, however, the fact that MQL cannot be used economically for all machining processes speaks against this type of coolant supply in machining. Therefore, the most suitable machining processes for minimum quantity lubrication are those in which lubrication is the primary concern (turning, milling, etc.). However, it is above all in grinding that this optimization of coolant wastage reaches its limits. One of the main reasons for this is that the lubricant aerosol cannot penetrate the air cushion that forms around the grinding wheel and thus cannot even reach the grinding gap. Furthermore, due to the small amount of coolant, there is an increased thermal risk because not enough coolant is used in the grinding process. But the design of the grinding machine and wheels also makes it difficult to equip them with channels. This is because minimal lubrication technology is divided into two systems: Systems with external MQL supply and with internal MQL supply. This means that with the use of minimum quantity lubrication, minimal or far-reaching changes must also be made to the machine tools and the tool so that this reduction in coolant can be implemented in the machining process.
Dry machining - grinding without coolant
This contrasts with the idea of an alternative: dry machining. At the present time and the state of the technology, it is not yet possible to carry out the grinding process without the supply of cooling lubricant. This is justified by the fact that the cooling lubricant has a positive influence on the thermal process for an optimally working grinding process with high performance and, on the other hand, the low scrap is essential.
By supplying the machining zone with cooling lubricant in a targeted manner, the process heat can be dissipated and
thus ensuring a grinding process free of grinding burns. Furthermore, not only the quantity of coolant, but also the orientation and design of the nozzles in the grinding process play a central role.
Conclusion
Especially in the field of machining with geometrically undefined cutting edge (grinding), a supply of cooling lubricant is of great relevance. Only with sufficient lubrication within the grinding process can a high quality finish of the workpiece be guaranteed.
Above all, to avoid grinding burn, it is important to provide sufficient cooling during grinding. This is very well possible without wasting huge amounts of
of coolant by optimizing the coolant supply to your machines.
You want to optimize your grinding process? We offer you process-optimized KSS nozzles that will help you to achieve this,
use the optimum amount of coolant in the grinding process.
Simply contact us at +49 (0)2273-95373 0 or send an e-mail to info@grindaix.de . We will be happy to advise you.
Products relevant to this article:
You may also be interested in these articles from our magazine:
Cool the grinding process properly
Cool the grinding process properly! This is easier said than done. We have compiled a list of the various parameters that need to be taken into account and which supply solutions are suitable or unsuitable here.
Cooling during grinding
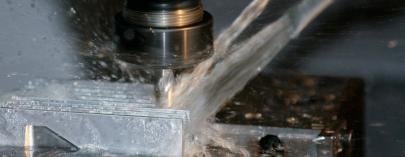
A great deal of heat is generated during grinding due to process-related friction. This heat must be reliably dissipated, which is why grinding processes require reliable cooling. You can read about what is important here.
Types of cooling lubricants
In addition to emulsions of different concentrations, in which various additives are used, the use of grinding oils is also common. We have compiled the areas of application, advantages and disadvantages, as well as the most important selection criteria for cooling lubricants for you.