Grinding technology - Overview of the interrelationships
Grinding technology covers all measures for machining surfaces with geometrically indeterminate cutting edge geometry of metallic and non-metallic components.
Grinding
The industrially used manufacturing process of grinding comprises various activities, which in turn are carried out by different assemblies of a machine tool.
Classification of activities
- Grinding tools
- Dressing tools
- Grinding process (machine kinematics)
- Component materials
- Cooling lubricant supply
The grinding result is based on economic (cycle time, set-up time, main time, machine hour rate, tool costs, costs for the use of cooling lubricant, ...) as well as technical target variables, such as surface quality, shape, dimensional and position tolerances, thermal edge zone influence (grinding burn), to name just a few of the key variables.
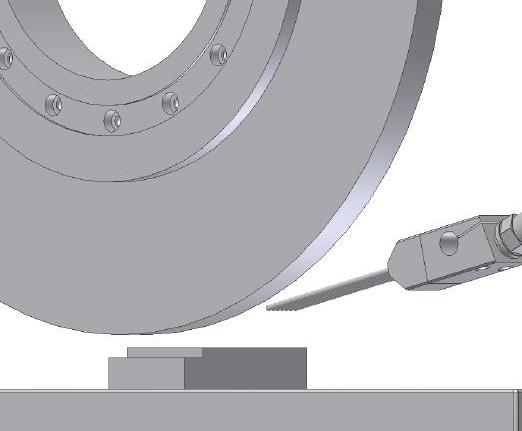
Robust processes are the goal
The correct choice of process parameters and tool specifications as well as the technical interaction of these different influencing groups on the grinding result represent the system complexity of the grinding production process. Some system variables, such as tool properties, are subject to dynamic change over the course of the process and wear out. The topography (surface condition) of the tools used and the macro-geometry (tool shape) are therefore constantly changing and alter the conditions of engagement during grinding and therefore also the process result. As a result, it is not possible to guarantee continuity of use of the system variable tool influence. The process is therefore subject to constant change in individual system variables, the scope for change of which must be mastered and controlled in order to guarantee process robustness in line with industrial standards as far as possible.
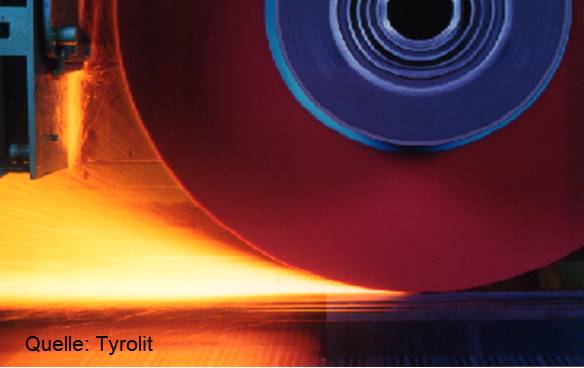
The right process parameters for grinding
While the process parameters (infeed, workpiece rotation, grinding wheel peripheral speed, feed rates, etc.) can be set reproducibly and very precisely over a sufficiently long period of time via the machine kinematics, the grinding process is subject to further fluctuations in the system variables due to possible variations in component geometry and composition. The smallest changes in the alloy composition of the component materials and deviations in the component geometry have consequences for the process result. In turn, the grinding tools and the process kinematics in the grinding process must be adapted accordingly. However, this is often not done automatically due to a lack of economically viable and technically robust monitoring options (e.g. of the grinding wheel topography) and is readjusted manually. This inevitably leads to sources of error and inefficiencies in operation - even in modern sanding systems.
The grinding result depends on many influencing factors
A comprehensive analysis of all influencing variables of the grinding technology is much more detailed and includes many other specific influencing factors for each influencing group mentioned, such as the choice of process parameters and their effect on the wear of the grinding tools used or the temperature development during grinding (e.g. grinding wheel dressed too finely or an insufficient supply of cooling lubricant).
Influencing factor cooling lubricant supply
Another significant influence on the process result (thermal edge zone damage, grinding burn, tool wear) is the cooling lubricant supply to the grinding process. If this is not targeted (point of impact of the coolant jet) and not designed to meet the requirements with regard to the process and tool geometry-specific supply quantity (l/min) and the associated coolant outlet speed (m/s), the quality specification of the component to be ground will not be achieved. Furthermore, the cooling lubricant supply represents the cooling of the machine components, which in turn can only guarantee kinematic accuracy and thus technical reproducibility of the process control variables via the machine tool if the heat flow is as constant as possible.
Conclusion
In summary, grinding technology can be described as a technical system with many different influencing factors that both change over time and are directly related to each other, thereby strongly influencing the required process results. The controllability of sanding systems requires a high degree of experience on the part of users and employees responsible for the process.
In this context, Grindaix GmbH focuses on the influencing factor of the cooling lubricant supply and ensures that its customers make as few mistakes as possible within this influencing group of grinding technology. The aim is always to achieve maximum process robustness with sufficient cost-effectiveness while complying with quality specifications. The Grindaix team will be happy to help you along the way.