The cooling lubricant supply
Cooling lubricants contribute significantly to the high performance level of numerous manufacturing processes. By removing process heat from the workpiece-tool contact point and reducing the heat generated by friction in the machining process, the metal removal rate of the machine tools can be increased, the service life of the tools can be extended and the quality of the workpieces can be improved. The use of cooling lubricants can therefore save costs and achieve better results at the same time.
Tasks of cooling lubricants
The tasks of cooling lubricants can be divided into primary and secondary tasks. As the name suggests, the primary tasks are lubrication and cooling:
The reduction of friction between the tool and the workpiece by forming a stable lubricating film.
In addition to the primary tasks, the cooling lubricant has other tasks to fulfill. The secondary tasks include:
Cleaning the tool and the workpiece from removed chips and dirt.
Removal of chips away from the machining area and the machine bed.
For the machine and the workpiece material.
Depending on the machining task, other tasks of the cooling lubricant are in the foreground, as the machining process is significantly influenced by the physical, chemical and biological properties of the cooling lubricants.
Challenges in the application of cooling lubricants
The use of cooling lubricant is very important when grinding in order to prevent damage to the component caused by grinding burn. However, there are challenges that need to be overcome when using cooling lubricants.
Cooling lubricant supply
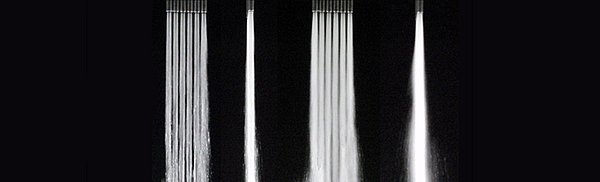
It is not the high quantity of cooling lubricant supplied to the machining zone that is decisive, but how much of it actually reaches the machining zone. It is therefore advisable to penetrate the air cushion rotating with the tool in order to reach the machining area with the cooling lubricant jet. The decisive reference value here is the exit speed of the cooling lubricant from the cooling lubricant nozzle. It is determined by the pressure upstream of the cooling lubricant nozzle. This must be adapted to the production process, otherwise thermal damage to the component will occur.
Grinding with cooling lubricant
High temperatures occur in the machining zone during grinding. These can be so high that they can cause thermal damage to both the workpiece and the grinding wheel. The result is a structural change, also known as “grinding burn”, in the workpiece edge zone. This leads to undesirable residual tensile stresses. These induce microcracks in the workpiece edge zone, which can lead to failure (breakage, etc.) when the dynamic load is applied during subsequent component use.
Thermal influences also have a negative effect on the tools. If the grain and bond material is not cooled properly, it is thermally overloaded to such an extent that the grinding tools wear out much faster. Both effects must be avoided. Therefore, a targeted and properly designed cooling lubricant supply is necessary.
Solution approaches
One approach to realizing an optimum cooling lubricant supply is to use cooling lubricant nozzles where the relationship between cooling lubricant outlet speed and cooling lubricant pressure is known. The nozzles can be used to direct a fast jet of cooling lubricant to the machining zone as required.
This requires precise positioning of the nozzle. If the cooling lubricant nozzle misses the machining zone by only a few millimetres, this leads to thermal damage to the tool and component. Therefore, suitable positioning aids (e.g. coolant-metal articulated hoses) are necessary. In addition, suitable measurement technology should be used to monitor the volume flow, pressure and lubricoolant outlet speed in order to adapt them to the requirements of your production process.
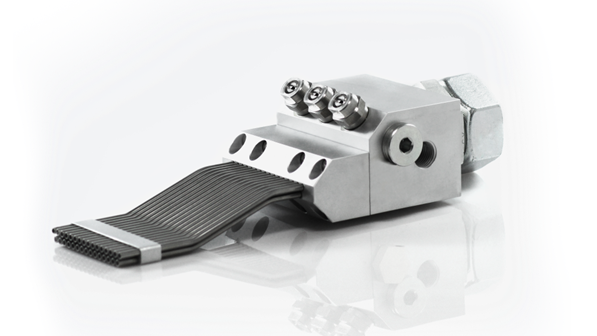
Sources: Klocke, F.; König, W.: Fertigungsverfahren 1 (2008); Klocke, F.; König, W.: Fertigungsverfahren 2 (2005); Richtlinie VDI 3397, Blatt 1 (2007)
Products relevant to this article:
You may also be interested in these articles from our magazine:
Cooling during grinding
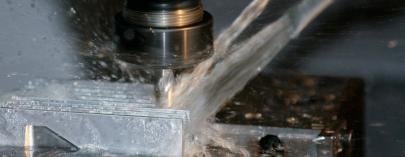
A great deal of heat is generated during grinding due to process-related friction. This heat must be reliably dissipated, which is why grinding processes require reliable cooling. You can read about what is important here.
Cool the grinding process properly
Cool the grinding process properly! This is easier said than done. We have compiled a list of the various parameters that need to be taken into account and which supply solutions are suitable or unsuitable here.
Grinding of components
Why are components ground and what options are available? In which cases is grinding necessary? We address these questions in our article “Grinding components”