Cooling lubricant nozzles from the 3D printer - an optimal solution?
Additive manufacturing with the help of 3D printing of metal components enables a completely new approach to the design and production of components. We at Grindaix have taken advantage of this fact to further improve our cooling lubricant nozzles, which are already successfully in use in a conventionally manufactured version. One particular aspect of our optimization is the adaptation of the nozzle to the required flow characteristics of the cooling lubricant.
3D printing as a manufacturing process offers a number of advantages that allow components to be designed and manufactured from scratch. However, some disadvantages must also be taken into account. We have presented the advantages and disadvantages, challenges and opportunities in our magazine article “Printing (3D) components”. In this article, we specifically address the optimization of our cooling lubricant supply systems with the help of 3D printing processes.

Optimized components through 3D printing for use in machine tools

With 3D printing, the shape follows the functional requirements. Manufacturing requirements, as they prevail in conventional manufacturing processes, do not have to be taken into account to the same extent. The resulting component optimization offers advantages in several respects, which, for example, also enable numerous improvements in the cooling lubricant nozzles used in machine tools - components can be better adapted to their function. Geometries and structures that were previously impossible to produce can be realized with 3D printing. Material and therefore weight can be saved through clever design and the use of optimized component structures.
Optimized coolant nozzles for internal cylindrical grinding
To illustrate the advantages of 3D printing, we compare our conventionally manufactured coolant nozzle for internal cylindrical grinding with our optimized 3D printed version. The internal cylindrical grinding process only offers very limited space for accommodating the coolant nozzle. At the same time, however, the coolant nozzle must be positioned as close as possible to the cutting point so that the cooling lubricant can be introduced into the machining zone in an optimal and targeted manner. Complex milling constructions with various holes were necessary in order to be able to design and manufacture a functional cooling lubricant nozzle for internal cylindrical grinding in the conventional way. Small grinding gap lengths can be adequately supplied with the full width of the conventional nozzle. However, long grinding gaps (high grinding wheel widths) cannot be supplied with the conventionally manufactured nozzle.
The new design of our coolant nozzle, specially geared towards production using 3D printing, has significantly improved many product properties and achieved advantages in production:
- The coolant nozzle was fully adapted to its function. The component geometry was determined on the basis of a detailed flow simulation to generate the optimum flow behavior of the coolant. Guide structures in the form of precisely adapted webs can also be incorporated into the component during 3D printing. In addition to optimizing the flow properties, the geometry of the component was also improved..
- Recesses and cavities as well as a low wall thickness enabled a considerable weight saving. Despite its filigree appearance, the coolant nozzle for internal cylindrical grinding is very rigid, making it possible to increase the supply width.
- Thanks to the high flexibility of 3D printing, specially adapted coolant nozzles can be designed for all machining tasks. Flexible adaptation (installation space/supply width) to various internal cylindrical grinding processes is possible.
Despite all the technical advantages of 3D printing, the disadvantages of the process must also be taken into account when planning production. In addition to the influence of temperature on the material, the price is also a decisive factor in the decision to use 3D printing. In most cases, this is many times higher than with conventional production. However, the cost savings when using conventional production come at the cost of losing many advantageous component properties.
Summary
3D printing is still in the development stage, but is gradually and increasingly establishing itself in industrial, professional applications. In addition to some disadvantages and necessary reworking of 3D printed components, 3D printing offers completely new flexibility in the design and manufacture of components.
Grindaix GmbH has also taken advantage of this to design cooling lubricant nozzles that are much more function-oriented. The form follows the function, manufacturing restrictions are reduced and better, tailor-made components can be realized.
Would you like to equip your machine tool with flow- and application-optimized coolant nozzles? We are your partner - because we combine our expertise in the field of lubricoolant supply in machine tools with professional flow simulation to achieve an optimum, application-oriented design for your cooling lubricant nozzles. For production, we cooperate with experienced 3D printing companies in the field of laser sintering.
You can find some examples of our 3D printed nozzles here.
If you are interested in an optimized (possibly 3D-printed) coolant nozzle, simply get in touch with our KSS professionals. We look forward to your inquiry!
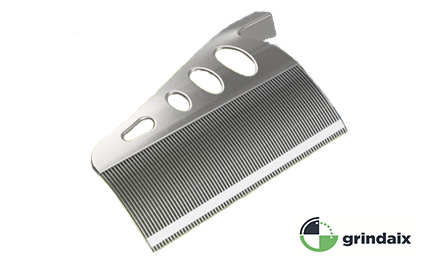
Products relevant to this article:
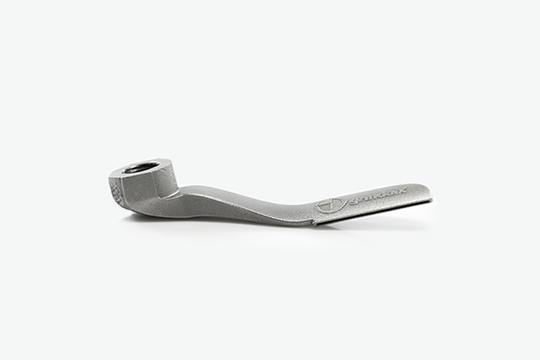
You may also be interested in these articles from our magazine:
Cooling lubricant supply
It is easy to understand that grinding processes need to be supplied with cooling lubricant. But what exactly does the cooling lubricant do and what are the challenges involved in supplying cooling lubricant?
Components (3D) printing
The generative production of components using 3D printing is becoming increasingly widespread in industry. In addition to the initial plastic printing processes, 3D printing in metal is now also possible. We have prepared a clear overview of the advantages and disadvantages for you.
Types of cooling lubricants
In addition to emulsions of different concentrations, in which various additives are used, the use of grinding oils is also common. We have compiled the areas of application, advantages and disadvantages, as well as the most important selection criteria for cooling lubricants for you.