Tool grinding - As demanding as the tools!
The term “Tool grinding” covers all machining tasks in which grinding wheels are used manually or on CNC grinding machines for tool machining to manufacture or overhaul a tool.
Tool grinding is a specialized area of component manufacturing on CNC grinding machines. The tools must meet very high accuracy requirements in order to be able to use them later. In order to achieve a long tool life at the same time, tools are made of very hard materials, which makes grinding more difficult. Examples of grinding operations are drills, milling cutters, saw blades or broaches.
Reasons for grinding tools
There can be just as many reasons for grinding different tools. However, the most common reasons are the manufacture and reworking or repair of tools:
Tools are already ground during manufacture in order to achieve the desired geometry of the cutting edge. Only then does a tool become ready to cut and can be used. In addition to the initial sharpening of a previously milled tool, production can also be carried out entirely on a grinding machine from bar stock.
As the tool is used, the cutting edges wear down and the desired geometry is lost. This results in reduced cutting ability and the tool becomes blunt. The original cutting ability of the tool can be restored by regrinding the cutting edge.
Challenges in tool grinding
A key challenge in tool grinding is the high hardness of the materials used, which makes machining more difficult. The grinding process exposes the tools to be ground to very high mechanical and thermal loads. As a result, there is a high risk of grinding burn. With the often cost-intensive materials used, rejects result in correspondingly high costs. Tools with grinding burn are unable to cope with the high mechanical demands, e.g. when milling metal components. Rapid loss of cutting ability or, in the worst case, breakage of the tool are possible consequences. For this reason, it is important to ensure that the tools are already in good condition when they are manufactured, which also applies to subsequent series production. The machining task must be reliably cooled.
Cooling during tool grinding
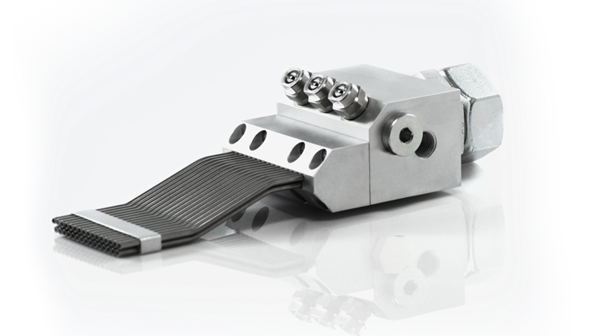
Tool grinding basically places the same demands on the lubricoolant supply as the subsequent component production with the tool. However, tool grinding usually involves more complex geometries that make it difficult to supply the grinding gap with an exact amount of lubricoolant. For this reason, complex, specially manufactured cooling lubricant nozzles often have to be used for tool grinding. An adapted and targeted lubricoolant supply forms the basis for a stable production process. We have prepared examples of cooling nozzles for tool grinding on our homepage.
Summary
Tool grinding is a special form of grinding due to the extremely hard tool materials and the abrasives and geometries used. At the same time, tool grinding places high demands on cooling, which can only be achieved using special nozzles adapted to the complex contours. Tool machining without grinding burns is essential to ensure a long tool life.