Grinding components
The term grinding refers to a manufacturing process in which high-hardness abrasive grains (cBN, corundum, SiC, diamond, ...) in bonded form (grinding tools) are used to shape a wide variety of materials (component materials) by removing chips.
Grinding is mainly used where there are high demands on the achievable surface quality of components (Rz, Ra, Rp0.2, Rmax). Due to the ever-increasing performance of grinding tools, grinding is also increasingly being used to achieve high cutting volumes.
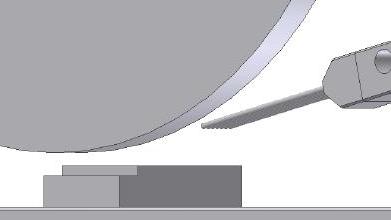
Problems and challenges when grinding

The ever-increasing demands on the achievable component qualities and the simultaneous shortening of cycle times are constantly presenting the grinding process with new challenges. The resulting increase in grinding performance leads to increased mechanical and thermal wear of the grinding tools (e.g. grinding wheels) as well as a higher energy input into the component edge zone, which in the worst cases can result in thermal damage to the components (workpieces) (microcracks, grinding burn).
The result: high tool costs, short dressing intervals, high reject rates. This results in higher production costs, which are often not accepted by the customer. This manufacturing dilemma has existed for many years and the industry has always responded with less wear-prone tool materials and improved process control (cycle optimization).
To proactively prevent the problems and challenges of grinding,
Grindaix GmbH has compiled a checklist with the "10 deadly sins of grinding burn prevention".
Get the checklist for free and avoid sanding burns!
Send us an e-mail now to schleifbrand@grindaix.de.
Factors that influence the grinding process
The number of influencing parameters for achieving a successful grinding process are very numerous and often indeterminable: Inhomogeneities of tool qualities, constantly changing dressing conditions/geometries due to wear (degrees of overlap, effective widths, dressing infeeds, ...), variances in process control (cutting speed, infeed, speed ratios, ...), use of cooling lubricants (oils, emulsions, solutions) and, above all, the use of outdated cooling lubricant supply systems (pipe, hose, sheet metal nozzles). Incorrect parameters lead to errors in the grinding process.
- Inhomogeneities of the tool qualities
- Dressing ratios/geometries
- Variances in process control
- Use of cooling lubricants
- Age of cooling lubricant supply systems
What does the Grindaix recommend?
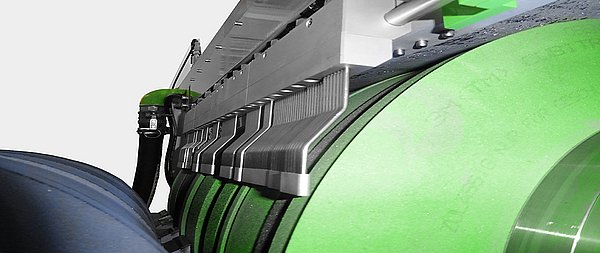
The supply of cooling lubricant has a decisive influence on the robust controllability and increased performance of grinding processes. Only precise knowledge and professional harmonization of the variables of cooling lubricant type, quantity, feed pressure, nozzle position, nozzle type, jet direction and outlet speed can guarantee an economical grinding process. Without the exact measurement and process-specific adjustability of these specific 7 influencing variables, a grinding process can only be determined empirically over a long period of time or operated sporadically at its real performance limits.
Grinding burn prevention is the core business of Grindaix.
We are familiar with the problems associated with grinding and will be happy to advise you on how to avoid grinding burn. If we have aroused your interest, please feel free to contact us: to the contact form
If you are interested in the topic of sanding burns, we will be happy to provide you with a free and non-binding checklist entitled “10 deadly sins when avoiding sanding burns”. The list contains 10 common mistakes when grinding and helps you to recognize and avoid them. To receive this checklist, please send us an e-mail to schleifbrand@grindaix.de.
Products relevant to this article:
You may also be interested in these articles from our magazine:
Tool grinding
Tool grinding is a particularly critical grinding application due to the special hardness of the workpiece. We have compiled a list of things to consider when grinding tools.
Grinding technology
Our article “Grinding technology” provides an overview of the complex topic of grinding technology with its many influencing factors. Here we offer you a complete overview of all relevant parameters.
Grinding wheels
The grinding wheel: is the tool within the grinding machine. Read here to find out how a grinding wheel is constructed, how it works and what to look out for when selecting grinding wheels and their properties.
CNC grinding machines
Grinding machines are state-of-the-art machining centers that are indispensable for producing a perfect surface finish today. Thanks to the use of computer-aided CNC controls, these high-performance machines also work fully automatically.