Grinding wheels - high-performance tools for grinding
A grinding wheel is a highly specialized tool that is usually used in grinding machines for precise hard-fine machining of metallic materials. Grinding wheels have developed into a high-performance tool in order to be able to comply with the high production tolerances during grinding and to achieve economical machining times.
Structure and materials of grinding wheels
Grinding wheels are rotationally symmetrical tools that are usually friction-locked to the drive spindle of a machine tool via a centric mount. A grinding wheel consists of a bond and the abrasive grains held in the bond. The abrasive grains are what make a grinding wheel capable of cutting in the first place, as abrasive grains break into splinters during engagement and thus constantly form new sharp edges that are capable of cutting. The abrasive grains used are usually differentiated according to their cutting properties or their hardness. They can be categorized as follows:
Classification of abrasives according to machinable materials:
For use on long-chipping, tough materials and particularly suitable for steel.
A corundum
B cubic boron nitride (cBN)
For use with short-chipping, brittle materials, e.g. for glass, ceramics, carbide (HM), gray cast iron (GG)
C Silicon carbide (SiC)
D Diamond
Classification of abrasives according to their hardness:
Conventional abrasives (“Conventional Abrasives”)
A Corundum
C Silicon carbide (SiC)
High-hardness abrasives (“superabrasives”)
B cubic boron nitride (cBN)
D Diamond
A distinction is made between natural abrasives (e.g. quartz or corundum) and synthetic abrasives such as silicon carbide (SiC), cubic boron nitride (cBN) or synthetically produced diamond. The application properties of grinding wheels can be specifically adjusted during production by adding certain additives and thus tailored to the respective application. For this purpose, certain fillers and additives are added, which can influence the heat resistance, toughness or strength, for example. Precision is particularly important in the production of the grinding wheel. The concentricity of a grinding wheel in particular must be perfect so that no unwanted vibrations affect the subsequent production process.
Requirements on grinding wheels
It is not without good reason that high demands are placed on grinding wheels and the entire grinding production process. When a component is ground, it has already undergone most of the necessary processing steps. This means that the damage caused by grinding burn or non-compliance with tolerances is particularly high. It is therefore important to avoid grinding burn, whereby the grinding burn-free process must also run at an appropriate processing speed in order to be economical. The grinding wheel plays a significant role in meeting these requirements for the grinding process. The main requirements for grinding wheels can be summarized as follows:
Service life
A grinding wheel is an expensive wearing part within the machine tool. For this reason, special attention is paid to the service life of the grinding wheel so that it does not have to be replaced frequently. Dressing, which is always used when the grinding wheel no longer has the specified shape or cutting ability, has a major influence on the service life. During dressing, part of the abrasive coating is removed in order to remove dirt or to make blunt abrasive grains cutable and therefore usable again by breaking them. Frequent dressing therefore leads to increased wear of the grinding wheel and undesirable non-productive times, as grinding cannot take place during dressing.
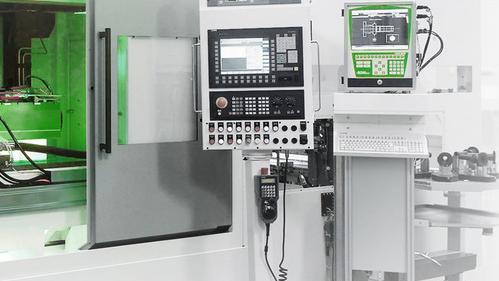
Cutting ability
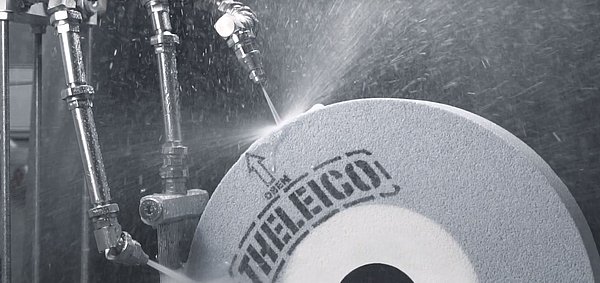
The abrasive grains protruding from the grinding wheel bond give a grinding wheel its cutting ability. However, contact with the material during grinding wears down these cutting abrasive grains, which reduces the cutting ability of the grinding wheel. The longer a grinding wheel can maintain the required cutting ability in the grinding process, the better for the economic efficiency of the process. The cutting ability of a grinding wheel can be influenced by the choice of grit material and the type of bond used, if this can then achieve a so-called self-sharpening of the grinding wheel. However, the cutting ability can also be restored by dressing, albeit with the disadvantages mentioned above.
Applicability
The grinding wheel used must be suitable for the material to be processed. Basic preliminary considerations must be made with regard to the existing bond, but also the abrasive used for the grinding wheel, the concentricity, the grinding quality to be achieved (abrasive grain concentration, average abrasive grain size, ...). As a rule, the grinding wheel manufacturers specify which grinding wheel is best suited for which application.
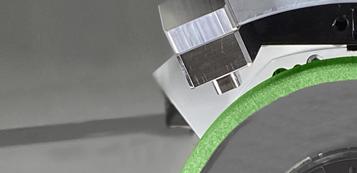
Mountability
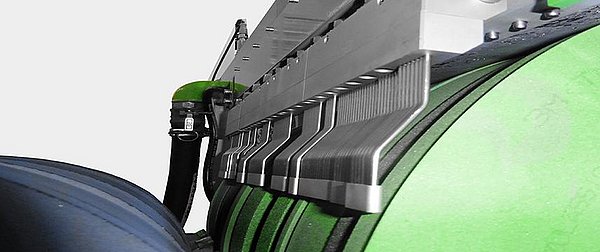
The selected grinding wheel must also match the machine mounting in the machine tool in terms of its dimensions and the intended connection dimensions. It must also be possible to attach additional elements such as cooling lubricant nozzles without colliding with the grinding wheel. Particular attention must be paid here to the required freedom of movement for loading equipment or other devices in the machine room.
Tasks of the grinding wheel bond
The task of a grinding wheel bond sounds quite trivial at first. The task of the grinding wheel bond is to keep the grinding wheel in its shape and the abrasive grains in the grinding wheel's microstructure. However, the tasks of the bond go far beyond this.
- Fixation of the abrasive grains in the bond matrix of the grinding wheel, but only as long as the cutting edges of a grain are capable of cutting.
- Detachment of the abrasive grain from the bond matrix of the grinding wheel as soon as the cutting edges of a grain are blunt. This is known as the self-sharpening effect.
- Ensuring sufficient self-wear. This serves to maintain the required grain protrusion.
- Protection against abrasive stress to ensure high profile accuracy of the grinding wheel.
- Dissipation of heat to prevent damage to the grain.
- Good profile properties to avoid unnecessary non-productive time (especially dressing).
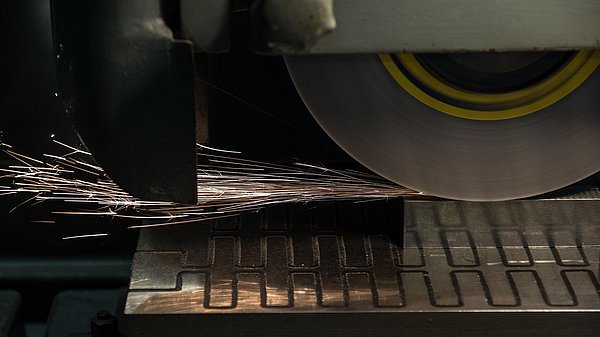
Common bonds for grinding wheels are made of ceramic, plastic or metal. The suitability of the grinding wheel for the material to be processed also depends on the type of bond used. Based on the bond, the following classification can be made according to the suitability of the material:
Galvanic bonds
Grinding wheels with an electroplated bond are generally suitable for grinding steel, hard metals, ferrite, CFRP, GFRP, synthetic resin, ceramics, semiconductor materials, quartz glass, graphite, artificial and natural stone, plaster, rubber and foodstuffs.
Sintered metal
Grinding wheels with a sintered metal bond are generally suitable for grinding glass, ceramics, semiconductor materials, silicon, precious stones, quartz, concrete, artificial and natural stone, gray cast iron, carbide formers, hard metals, hard ferrites.
Plastic
Grinding wheels with a plastic bond are generally suitable for grinding hard metals, ceramics, glass, quartz, carbide formers, steel and stellite.
Ceramics
Alloyed and unalloyed steels, high-speed steels, cast materials, Ni-based alloys, non-ferrous metals, sintered metals, polycrystalline diamond (PCD).
Application and process
Grinding wheels are used in almost all grinding processes. As a wide variety of grinding processes are used on machine tools, various grinding wheel geometries are available from a wide range of manufacturers. From the standard grinding wheel for external cylindrical grinding to cut-off wheels for use on hand-held machines and cup grinding wheels, almost all grinding wheel shapes are available.
Interactions between grinding wheel and cooling lubricant
Within the machine tool, the function, service life and reliability of the grinding wheel and the entire process depend on many different factors and their interactions. The interactions between the component, grinding wheel and cooling lubricant will be examined in more detail here, as the targeted and precise use of cooling lubricant can achieve maximum productivity for the grinding wheel and therefore the grinding machine:
Thermal influences
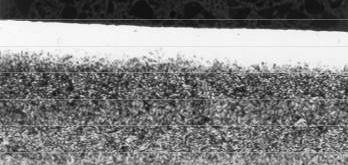
A large amount of heat energy is generated during grinding due to friction. Around 92% of the process energy is present as frictional heat and must be dissipated. Otherwise, undesirable damage to the component (e.g. grinding burn) can occur, leading to expensive component rejects. In addition, excessive thermal stress is likely to damage the grinding wheel (abrasive grains or bond), leading to premature tool failure and therefore higher wear costs. Both problems must be avoided in order to maximize the productivity of the grinding process.
Temperatures and cooling lubricant supply
Cooling lubricant is used to dissipate the temperature from the machining zone. It is particularly important to supply cooling lubricant to the machining zone in a targeted and needs-based manner in order to achieve particularly efficient and functional cooling. If too much cooling lubricant is used, a high fluid pressure is created between the grinding tool and the component, known colloquially as the “aquaplaning effect”, which can have a negative impact on the roundness of the component. If, on the other hand, too little cooling lubricant enters the machining zone, the process heat can only be dissipated inadequately. The thermal energy generated by the friction during grinding can lead to thermal damage to the component if it is not dissipated with the chip or the cooling lubricant, but via the component edge zone. The temperatures that occur are often so high that grinding burn occurs on ground components. Grinding burn is thermal edge zone damage to the component, which has a significant negative impact on the subsequent function of the component and can therefore lead to the component being rejected. This costs money and time and should therefore be avoided at all costs. Optimum interaction between the grinding wheel, its peripheral speed and the exit speed of the cooling lubricant from the nozzle are essential factors for sufficient cooling of the machining task. The correct setting of these parameters can be precisely adjusted and monitored using suitable measuring and control systems. The Coolant Pointer and the Coolant Display from Grindaix, for example, are suitable for this purpose.
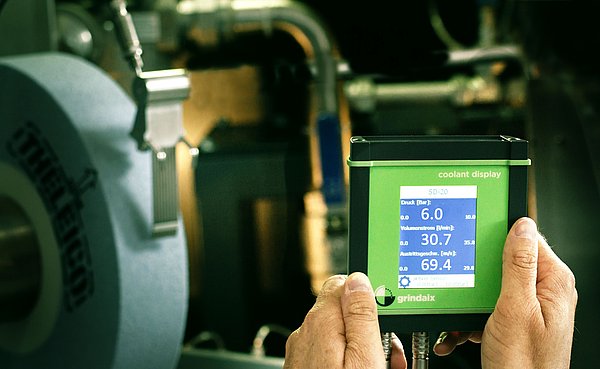
Conclusion
The flawless, economical and reliable function of a grinding wheel depends on a wide variety of factors. First of all, basic requirements and the right choice of grinding wheel play a role in the correct set-up of the “grinding” machining task. A wide range of parameters are relevant in order to optimize the process and trim it for maximum efficiency. In order to determine these parameters correctly, a simple trial and error approach is not efficient for this demanding process and is often not effective. Correct tuning can only be carried out successfully with the appropriate experience and taking into account many important dependencies and interrelationships.
As an experienced cooling lubricant system service provider, Grindaix GmbH will support you in this optimization or troubleshooting of your grinding task with a great deal of know-how and professional manufacturing expertise. We have already been able to optimize several thousand grinding burn-prone processes and thus significantly reduce the cycle time of the manufacturing process for our customers while at the same time avoiding grinding burns. This has increased economic efficiency. The products from Grindaix GmbH make the handling of your cooling lubricant system more efficient, robust and predictable. We have a comprehensive range of cooling lubricant nozzles as well as measuring and control systems available for you.
Please feel free to contact us - we look forward to hearing from you!
Products relevant to this article:
You may also be interested in these articles from our magazine:
Tool grinding
Tool grinding is a particularly critical grinding application due to the special hardness of the workpiece. We have compiled a list of things to consider when grinding tools.
Grinding technology
Our article “Grinding technology” provides an overview of the complex topic of grinding technology with its many influencing factors. Here we offer you a complete overview of all relevant parameters.
Grinding of components
Why are components ground and what options are available? In which cases is grinding necessary? We address these questions in our article “Grinding components”
CNC grinding machines
Grinding machines are state-of-the-art machining centers that are indispensable for producing a perfect surface finish today. Thanks to the use of computer-aided CNC controls, these high-performance machines also work fully automatically.