Coolant lubricant tubes – Overview of the models available
For the supply of coolant lubricant within the grinding machine, coolant lubricant tubes are used. These supply coolant lubricant from the machine connection to the nozzle. Depending on the design of the supply system, various coolant lubricant tubes made of different materials are available. The reliability of coolant lubricant supply is decisive to part quality during grinding and other machining processes. For this reason, the supply of coolant lubricant via coolant lubricant tubes must be robust and easy to handle.
In the following, we will compare the most important features of coolant lubricant tubes, weigh up the advantages and disadvantages of each type and provide tips on selection and use.
Application areas of coolant lubricant tubes
Within a grinding machine, the coolant lubricant flow usually splits up for use in various areas of the grinding machine. Some of the coolant lubricant is used for process cooling at the grinding site, for instance, while some is used for tool cleaning, bed flushing or for cleaning the part and measuring devices.
To apply the coolant lubricant in the right places, an efficient coolant lubricant supply system up to the nozzle is required within the working area of the machine tool. This is mostly achieved with different types of coolant lubricant tubes, as these allow (more or less) precise positioning of the nozzle, so that the coolant lubricant does not need to be sprayed across long distances.
Another purpose of the coolant lubricant tube is to ensure that a coolant nozzle is correctly positioned and supplied with coolant lubricant. To achieve this, the connection dimensions of the nozzle and the supply connection on the machine tool must be selected appropriately.
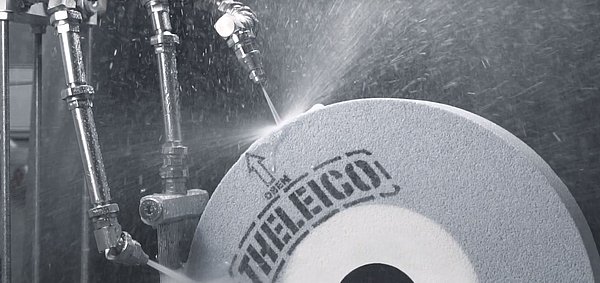
As the coolant lubricant tubes are installed in the working area of grinding machine, they themselves often need to withstand abrasive wear influences, such as from flying chips (spark jets) and from frequently over-contaminated coolant lubricant. The coolant lubricant tubes used in machine tools must therefore be particularly robust and resilient.
Coolant lubricant tubes designs
Coolant tubes are available in various designs. As there are numerous options that need to be taken into account when selecting a coolant hose, we offer you a brief overview of the most common feed solutions for coolant in grinding machines below:
Tubes
The simplest self-made solution for supplying cooling lubricant (coolant supply). The cooling lubricant is fed through pipes, often of any cross-section, in the direction of the cutting point. In order to generate a higher outlet speed, the pipe ends of metal pipes are pinched shut. This solution can usually be implemented cost-effectively, but this design is usually very rigid and inflexible.
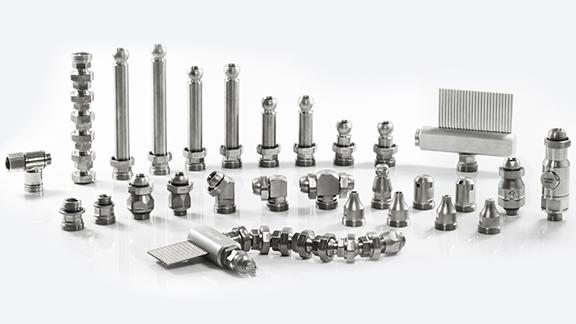
Hoses
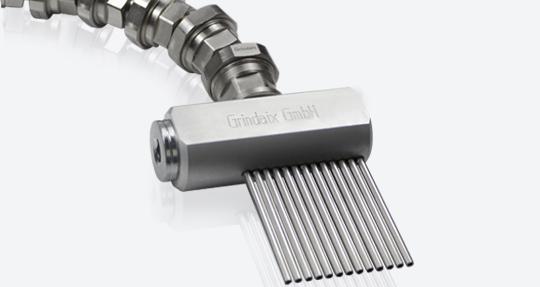
Another simple solution is to attach flexible rubber hoses, which must be additionally fixed at any point within the machine tool. Metal-coated rubber hoses can also be used to increase the service life. Hoses are not dimensionally stable and therefore do not retain their position. Additional fastening of the nozzle mounted at the end of the hose is therefore necessary so that the cooling lubricant can be supplied at the correct point.
Articulated hoses
The articulated coolant hose is a very frequently used feed solution for supplying cooling lubricant in machine tools. Manufactured from metal or plastic, articulated hoses are resistant to cooling lubricant. Joints, which are used at regular intervals along the length of the hose and plugged together, allow maximum flexibility in the shape of the coolant supply. Depending on the design, articulated hoses are tight and, depending on the type of joint and hose, are more or less positionally stable up to a certain coolant lubricant pressure and are available in all standard connection dimensions. Some plastic articulated hoses are usually even equipped with universal nozzles, which can be used for simple coolant supply.
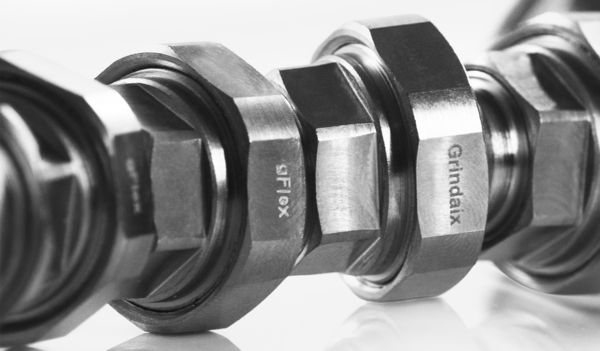
Material selection
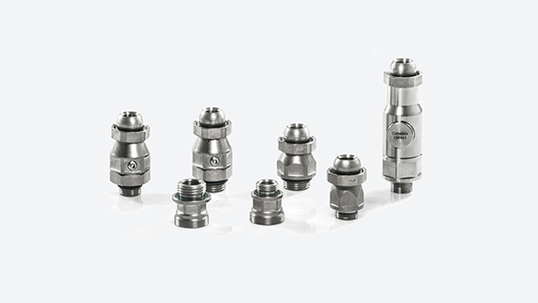
The material used for articulated hose systems has a decisive influence on the functional properties, durability and price. We have clearly compared the most important properties of articulated hose systems for metal and plastic versions. Basically, the plastic coolant articulated hose is considerably cheaper than a metal version. Due to the low price, however, some functional properties of the plastic articulated hose are less well fulfilled than is the case with the metal articulated hose. Due to the considerably longer service life, the metal articulated coolant hose compensates for part of its purchase price through its longer service life.
Comparison of metal vs. plastic articulated hose
Property
Pressure stability |
Position stability |
Durability |
Flexibility |
Price |
Metal articulated hose
+ |
+ |
++ |
+ |
- |
Plastic articulated hose
- |
- |
- |
++ |
++ |
Meets the requirements in comparison: ++ much better; +better; o similar; - worse; -- much worse
Articulated metal hose: Combines the best properties
A particularly resistant and flexible coolant supply can be realized with metal articulated coolant hoses. Metal articulated hoses are primarily used to supply cooling lubricant and can reliably maintain the nozzle position even in high pressure ranges. Metal articulated hoses can be flexibly adjusted at each individual joint and then screwed into the desired position. This allows almost unlimited flexibility in the supply of cooling lubricant within the machine tool. Metal articulated hoses guarantee positional stability up to a cooling lubricant system pressure of 50 bar, for example, and therefore more than the other cooling lubricant supply systems made of plastic. However, metal articulated hose systems are more expensive to purchase than other cooling lubricant supply systems. In return, metal articulated hoses combine the advantages of flexible rubber hoses and robust metal pipes.
gFlex
With the gFlex system, Grindaix GmbH offers an articulated metal hose system specially developed for grinding technology. The gFlex articulated metal hose system is an equally modular, expandable and ergonomic articulated metal hose for supplying cooling lubricant to your grinding machine. All elements of the gFlex metal articulated hose are mechanically pre-inhibited so that the metal articulated hose can be easily aligned and installed even when not screwed in place. The pressure and flow losses have been optimized for all bending radii and shape flexibilities, and dirt deposits are reduced by optimizing the geometry. There is a separate characteristic curve for each hose type in relation to the cooling lubricant volume flow and the flow resistance - for each joint, for each nozzle and for any extension module.
The gFlex metal articulated coolant hose system comes with an extensive range of accessories, including machine connections of all standard connection sizes, quick-change systems, sensors (pressure, flow rate, temperature) and a wide variety of Grindaix nozzles, all the components required for successful coolant supply in grinding machines.
The metal articulated hose gFlex is a very comprehensive cooling lubricant supply system that enables a quickly variable and user-friendly cooling lubricant supply in your grinding machine.
Products relevant to this article:
You may also be interested in these articles from our magazine:
Cooling lubricant supply
It is easy to understand that grinding processes need to be supplied with cooling lubricant. But what exactly does the cooling lubricant do and what are the challenges involved in supplying cooling lubricant?
Cooling lubricant nozzles
Cooling lubricant nozzles generate the necessary outlet speed of the coolant. However, nozzles are not only required for cooling applications. You can find an overview of all applications and designs here.
Cooling during grinding
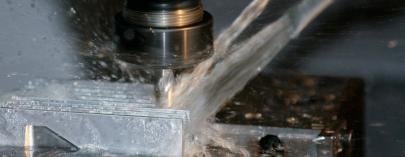
A great deal of heat is generated during grinding due to process-related friction. This heat must be reliably dissipated, which is why grinding processes require reliable cooling. You can read about what is important here.