Cleaning of cooling lubricant
Cooling lubricantis an important component of industrial production with CNC machine tools. The cooling lubricant cools and lubricates the machining task and thus enables economical and reliable production operations. However, as the cooling lubricant is introduced directly into the machining gap in order to cool it as well as possible, it also becomes contaminated in the process. Machining residues such as metal chips, grinding dust and tool abrasion collect in the cooling lubricant. These machining residues in the cooling lubricant damage the cooling lubricant system units (such as pumps, valves, coolers or nozzles) through abrasive wear or clogging. In addition, the desired machining result may no longer be achieved with contaminated coolant, e.g. if a high surface quality is required.
Cooling lubricant filtration systems are used so that these contaminants can be removed from the cooling lubricant with the required level of purity. If a suitably efficient filtration system is used in a production facility, this reduces wear on system components and extends the service life of the cooling lubricant. Lubricoolant filtration has a particularly positive effect on the reliability of the machining task. Correctly dimensioned lubricoolant filtration is important for smooth production with consistent machining quality, low lubricoolant system component wear and low production downtime.
Challenges in cooling lubricant cleaning
The filtration of cooling lubricants presents its own unique challenges. The most important requirement for filtration is first and foremost to provide the required volume flow with the necessary purity. The purity of cooling lubricants is specified on the basis of NAS 1638 or ISO 4406. The difficulty with cooling lubricant filtration is ensuring the required purity despite fluctuating dirt loads, different volume flows and clogging filter materials.
The correct dimensioning of the filtration system is a fundamental prerequisite for achieving these goals when planning a production line. Regular monitoring of the cleaning performance of the cooling lubricant filtration system during operation is also essential.
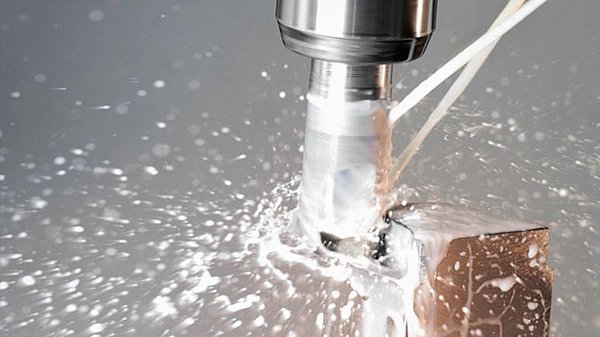
Options for cleaning cooling lubricant
There are various methods available for cleaning cooling lubricants. The decisive factors for selecting a filtration method are the required cooling lubricant purity and the required volume flow (l/min). Some common filtration methods are briefly described below:
During sedimentation, the contaminated cooling lubricant is collected in a container in which the solid contaminant particles settle to the bottom due to gravity. The cooling lubricant cleaned in this way can be removed from the top, while the sedimented dirt is discharged from the bottom of the container using a scraper belt conveyor.
During centrifuging, the contaminated cooling lubricant is fed into a rotating drum in which the centrifugal forces separate the solid contaminant particles from the liquid cooling lubricant. Frequently used centrifuges for coolant lubricant cleaning are, for example, disk separators.
During filtration, the contaminated cooling lubricant is passed through a porous filter medium, which binds the solid contaminant particles and allows the liquid cooling lubricant to flow through. The filter medium can be designed as a belt, drum or cartridge. When using backwash filters, however, cooling lubricant may be discharged from the cooling lubricant system. These lost quantities must be replaced or topped up occasionally.
In magnetic separation, the solid contamination particles are magnetized and thus separated from the liquid cooling lubricant. For this process to be applicable, the contamination particles must be magnetic material. The highly abrasive wear particles from the grinding wheel must also be filtered out of the cooling lubricant, but are not magnetic.
Would you like to know more about the manufacturing processes mentioned?
In our magazine article “Cooling lubricant filtration systems” you will find an even more detailed description of the individual processes.
Please feel free to take a look.
Costs for cleaning cooling lubricant
The maintenance of cooling lubricant is expensive, as several steps are necessary in various systems to prepare the cooling lubricant for reuse. The largest operating costs, in addition to the purchase of the cooling lubricant filtration system, are broken down below:
To reduce the above-mentioned costs, it is advisable to reduce the total throughput of cooling lubricant. This reduces the load on filters, pumps consume less energy and a lower total quantity of coolant lubricant may be required. There is potential for optimization in almost every production process. In the long term, many costs can be saved if the lubricoolant supply and filtration are tailored to requirements.
Cooling lubricant is pumped from the filtration system to the processing machine and back through pipes. These tasks are performed by powerful pumps that provide the required pressure and volume flow. These pumps are driven by electric motors, which consume large amounts of energy according to their performance. Additional motors may be required in the filtration system itself, e.g. to drive centrifuges.
Filter aids are auxiliary materials that are used to achieve the desired filtration result. Filter aids are used up and must be procured accordingly. Filter cartridges, for example, need to be replaced after a certain period of use.
Even with the best care and filtration, the cooling lubric ant is subject to ageing and must be replaced after a certain period of use, depending on the load. In addition to the procurement of new coolant lubricant, the old coolant lubricant must be disposed of at great expense.
Summary
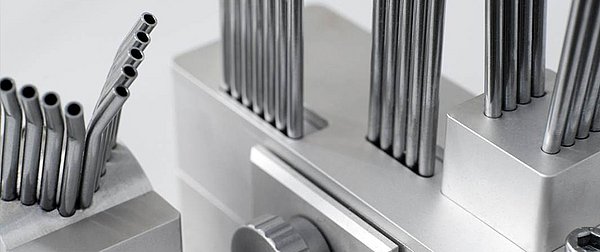
Cooling lubricant filtration (or preparation) is an indispensable component of the cooling lubricant system for maintaining the cooling lubricant supply with the required purity and volume flow. Various processes are available for the filtration of the cooling lubricant, which must be selected and dimensioned according to the existing requirements in production. As a treatment measure, the filtration of cooling lubricant causes a considerable proportion of the cooling lubricant-related costs, as energy and filter aids are consumed.
Benefit from our knowledge
Is cooling lubricant filtration a “black box” for you or are you experiencing problems in your production? We can help you! As an experienced cooling lubricant system service provider, Grindaix GmbH brings know-how from numerous successful optimization projects.
Get in touch with us - our specialists will be happy to advise you on the preparation of your cooling lubricant!
Products relevant to this article:
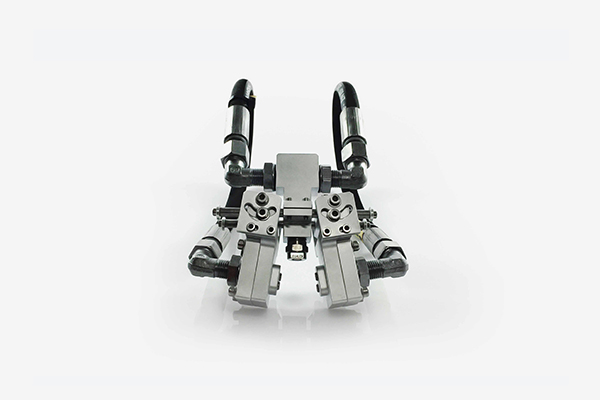