Finding and rectifying faults in the cooling lubricant system
Modern large-scale production of metallic components often involves large and equally complex cooling lubricant systems that are used to supply the existing machine tools. These systems are part of the necessary infrastructure of a manufacturing company, roughly comparable to electricity, water or compressed air.
This inevitably means that the coolant systems must reliably and consistently fulfill their function of adequately supplying the connected machine tools with cooling lubricant in the required quantity and at the required pressure. The operational readiness of entire production lines often depends on this.
Consequently, a failure of the cooling lubricant supply system, for example, endangers further production and, in the worst case, can lead to an interruption in component production. In such cases, the reason for the system failure must be found quickly, because every minute of downtime for a production system, even if it is only for the time needed to rectify the fault, results in immense downtime costs for the operator.
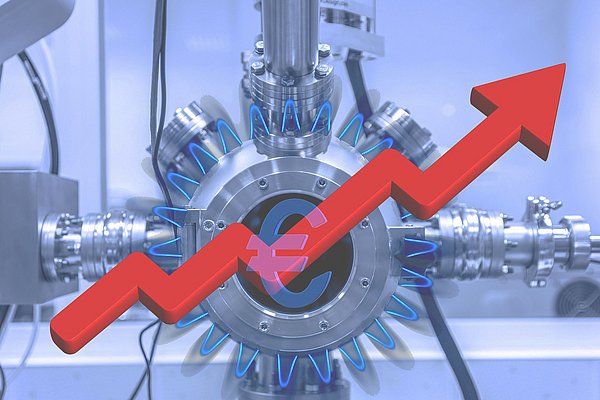
Causes of failure
In addition to pipelines, a cooling lubricant system consists of many mechanical components such as pumps, valves or filtration elements. These have the potential for defect due to component failure. In addition, a cooling lubricant system is operated with a relatively aggressive medium, the cooling lubricant. Machining residues and the finest particles of contamination cause so-called abrasive wear on almost all components that come into contact with the cooling lubricant.
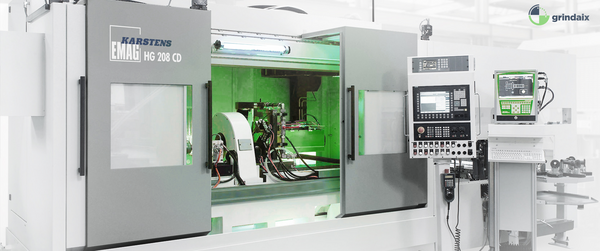
As the size of a system increases, so does its complexity. Piping networks become confusing and the system as a whole can no longer be overseen. This circumstance creates further potential for malfunctions in cooling lubricant systems. If additional process variables are changed in an existing system, e.g. a higher cooling lubricant volume flow is absorbed by a machine tool, the pressure and the dependent pipe friction losses within the cooling lubricant change. Such changes can also cause problems at other points in the cooling lubricant system due to insufficient cooling lubricant volume flows or pressures. The connected machine tools are no longer optimally supplied. In addition, if the flow rate falls below a certain level in the pipe, there is a risk of deposits of solids carried in the cooling lubricant. The flow rate should not fall below 2 m/s if possible.
Find the causes of defects
If a fault occurs in the cooling lubricant system during operation, it is often not possible to find and rectify the fault in a targeted manner (unless the cooling lubricant leaks out at a fault point). This is because the complexity of the cooling lubricant system makes it difficult to locate a fault.
In the already complex piping system of the cooling lubricant system, there are many influencing factors whose effects only arise or intensify over time, e.g. due to the deposition of machining residues in the piping system. Furthermore, many cooling lubricant systems often have inadequate monitoring options that could help to localize the cause of a fault. Any changes made, e.g. adding pipe sections or changing the operating conditions on which the system design is based, make a precise fault analysis even more difficult.
The consequences are often similar. The connected machine tools are not supplied with the required quantity of coolant (flow rate) and pressure, as intended in the planning of the system. This is not yet a complete system failure, but there are still significant effects on the operating conditions of the connected machine tools and their process parameters.
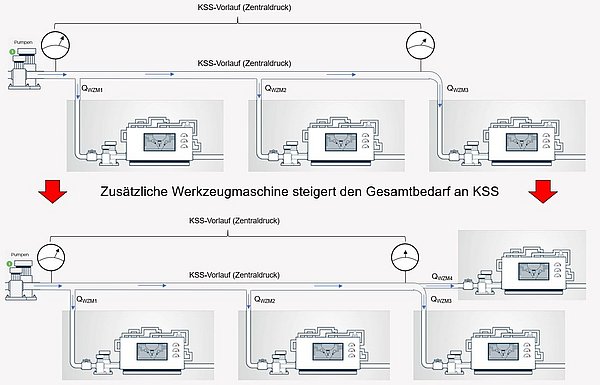
Faults such as a cooling lubricant pump breaking down, a valve getting stuck or a pipe becoming blocked can, in the worst case, lead to an interruption in the cooling lubricant supply. The connected machine tools will no longer be supplied with cooling lubricant, which will inevitably result in an interruption of production. In such cases, it is necessary to find the cause quickly so that production can continue without delay. However, finding the component that is causing a fault is difficult due to a lack of data and knowledge and is only possible with a great deal of knowledge and experience of the CL system in question.
Simplify troubleshooting
Adequate troubleshooting of a cooling lubricant system begins even before a fault has occurred. Determining operating parameters in the cooling lubricant system (e.g. pressures, volume flows, temperatures, etc.) enables the operating conditions in a cooling lubricant system to be evaluated over time. Consequently, it is possible to determine changes that occur over time in the cooling lubricant system. In addition, experience can be gained as to whether certain parameters indicate faults and malfunctions that occur. This makes it possible to take targeted action to prevent a failure.
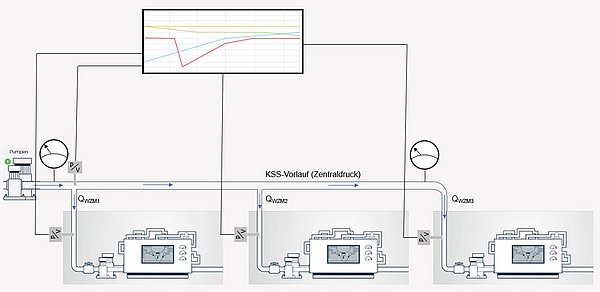
When recording operating parameters in a cooling lubricant system, measurement technology that is adapted to the application in a cooling lubricant system and can be implemented as a coolant monitoring system in the existing system helps.
Continuous monitoring and evaluation of the measured values from the cooling lubricant system allows a statement to be made about its condition at any time. If the values deviate from the norm, quick and targeted measures can be taken to rectify the problem. In addition, individual components of the cooling lubricant system can also be monitored. If, for example, the required central pressure in the cooling lubricant supply line is no longer reached, there could be a problem with the supply pump or the downstream piping.
Another way to keep track of a cooling lubricant system is to continuously document the system. When the system is put into operation, the documentation is provided by the manufacturer. If changes are made to the cooling lubricant system over time, these should be added to the documentation so that the function of individual components and lines can be traced at any time.
Summary
A cooling lubricant system is responsible for supplying the connected machine tools and is therefore a basic requirement for a smooth production process. Depending on their size, cooling lubricant systems can take on complex dimensions, making it difficult to maintain an overview of the entire system. This also makes troubleshooting more difficult and usually costs a lot of time, during which no production takes place.
In addition to the documentation of cooling lubricant systems, cooling lubricant monitoring systems can also be used to support this. Cooling lubricant monitoring systems take over the metrological monitoring of a cooling lubricant system. This allows important operating parameters to be permanently monitored. These include, for example, pressures, volume flows and temperatures, but also pH values, dirt loads and other relevant measured variables. A CL monitoring system enables comprehensive monitoring of the CL system, which results in significant gains in the reliability of a CL system. Targeted maintenance of individual components of the CL system is also possible.
Products relevant to this article:
You may also be interested in these articles from our magazine:
Cleaning of cooling lubricant
Why does cooling lubricant need to be cleaned and what options are there for this? What needs to be considered and where is there potential for increasing efficiency? You can read this and other interesting facts about cooling lubricant cleaning here.
Coolant lubricant tubes
Coolant lubricant tubes are commonly used to conduct cooling lubricant in the machine tool. However, not all types of these tubes are suitable for every application. We provide an overview of the possibilities of coolant supply with Coolant lubricant tubes.
Types of cooling lubricants
In addition to emulsions of different concentrations, in which various additives are used, the use of grinding oils is also common. We have compiled the areas of application, advantages and disadvantages, as well as the most important selection criteria for cooling lubricants for you.
Coolant filtration systems
Treatment is a crucial part of the cooling lubricant supply with a major impact on production results and efficiency. We have described and compared the usual filtration processes for cooling lubricants.