The free jet of a cooling lubricant nozzle
Liquid jets can be categorized as free jets. Free jets are categorized as either laminar or turbulent. The exit velocity of cooling lubricant in grinding technology is high. A resulting variable of the high exit speed is a Reynolds number greater than 2300. Therefore, cooling lubricant nozzles are always turbulent free jets. The turbulent free jet is a typical flow process of a nozzle. [1,2,3]
In addition to the turbulence of the free jet, the type of flow phenomenon is also distinguished. Since the ambient medium of a cooling lubricant nozzle is still air, the free jet can be classified in the group of free turbulence. Figure 1 shows the basic structure of a free jet with its characteristic areas. [1,2,3]
The free jet divides into several areas depending on the distance and position relative to the nozzle outlet. The following areas are distinguished:
- primary fluid
- secondary fluid
- core
- mixing zone
The fundamental formation of a free jet can be divided into several points. First, the primary fluid (cooling lubricant) flows out of an opening at a speed c0 into a secondary fluid (air).

The secondary fluid (air) is a stationary surrounding medium without a sharp boundary surface. This is to be distinguished from wall turbulence, in which the surrounding is a fixed boundary without exchange. [1,2,3]
A relative movement occurs between the primary fluid and the stationary secondary fluid because both media have different velocities. The boundary surface is called the boundary layer. Friction between the boundary zone of the primary fluid and the boundary zone of the secondary fluid causes the secondary fluid to be entrained. As a result, the boundary zone of the primary fluid mixes and becomes enriched with the secondary fluid. [1,2,3]
The core area is characterized by the fact that it consists of an undisturbed flow. The core area decreases conically with increasing distance from the outlet opening. The influence of the secondary fluid increases with increasing distance from the outlet and mixes with the core area. The length of the core area is not in any fixed ratio to the outlet geometry, but depends largely on the internal design of the nozzle. Immediately behind the nozzle outlet, the velocity of the primary fluid is constant. [1,2,3]
In the mixing zone, also known as the transition zone, the secondary fluid increasingly mixes with the primary fluid of the nozzle. The velocity decreases hyperbolically with increasing distance from the outlet opening in the x-direction (see Figure 2). The decrease in velocity is caused by the internal friction of the fluid mixture. [1,2,3] In the y-direction of the free jet, a velocity profile forms according to a Gaussian normal distribution. The boundary zone of the free jet has a velocity of zero and thus equalizes with the velocity of the secondary fluid. The pressure in the entire free jet is ambient pressure. [1,2,3]
The jet break-up of a cooling lubricant nozzle
Immediately after the free jet flows out of the nozzle at a defined speed, it begins to disintegrate. The fluid disintegration depends on several factors. These include, among other things:
- the internal shape of the nozzle
- the material data of the fluid and the ambient medium
- the relative speed between the fluid and the environment.
These influencing variables determine the degree of atomization and thus the size distribution of the resulting droplets. In addition, these variables determine the characteristic length of the core area.
Decay mechanisms of the cooling lubricant free jet
In the publication, a distinction is made between different break-up mechanisms of the free jet.
These disintegration mechanisms have been experimentally recognized and defined. The following are distinguished:
- Droplet disintegration (Rayleigh disintegration)
- Wave disintegration
- first wind-induced range
- second wind-induced range - Atomization
The disintegration mechanisms mentioned above are schematically (left) and experimentally (right) depicted in Figure 2.
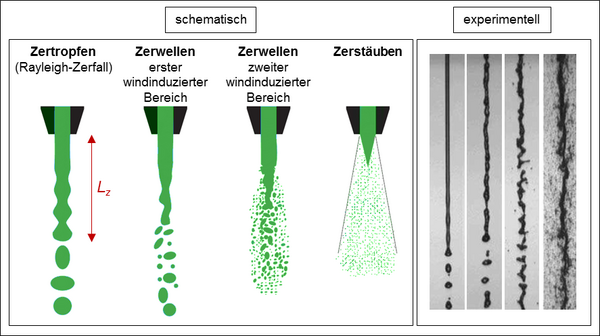
The fluid cylinder emerging from the nozzle is unstable and eventually leads to the break-up of individual drops due to axial-symmetrical vibrations of the liquid surface. This break-up mechanism is also called Rayleigh break-up and occurs at very low flow velocities. The detached droplets are larger than the original jet diameter. Of all the break-up mechanisms, the jet break-up length Lz, i.e. the length relative to the nozzle exit from which the droplet detaches, is the longest and decreases with increasing flow velocity. [5,6]
First wind-induced length
Increasing the flow velocity from the nozzle accelerates Rayleigh decay through axially symmetrical oscillations. The droplets separate from the fluid jet earlier, leading to smaller droplets with the size of the original jet diameter. The earlier separation of the droplets reduces the jet decay length Lz. [5,6]
Second wind-induced area
If the flow velocity is increased further, the Rayleigh decay and thus the axially symmetrical vibrations are intensified. This results in droplets that are smaller than the original jet diameter. The jet decay length Lz shifts further towards the nozzle exit. [5,6]
The droplet detachment begins immediately after leaving the nozzle outlet. A spray of small droplets is formed. The size of the droplet size distribution varies greatly and is considerably smaller than the original jet diameter. Depending on the nozzle geometry, there may be a core area of the free jet. [5,6]
Do you need support from an expert in this field? Then please do not hesitate to contact us. We will analyze your grinding process and offer you a customized solution.
Sources:
[1] Oertel jr., Herbert (Hrsg.): Prandtl - Führer durch die Strömungslehre: Grundlagen und Phänomene, 14. Aufl. 2017, Wiesbaden, s.l., Springer Fachmedien Wiesbaden, 2017 (Springer Reference Technik).
[2] Schlichting, Hermann; Gersten, Klaus; Krause, Egon: Grenzschicht-Theorie: Mit 22 Tabellen, 10., überarbeitete Auflage, Berlin, Heidelberg, Springer-Verlag Berlin Heidelberg, 2006.
[3] Glazik, Günter; Kraatz, Willi; Kranawettreiser, Jörg; Martin, Helmut; Wagner, Harold: Technische Hydromechanik, 2., vollständig überarbeitete Auflage, Aigner, Detlef (Hrsg.); Carstensen, Dirk (Hrsg.), Berlin, Wien, Zürich, Beuth Verlag GmbH, 2015.
[4] Kümmel, Wolfgang, Technische Strömumgsmechanik, Theorie und Praxis, B.G. Teubner Verlag / GWV Fachverlage GmbH, Wiesbaden 2007.
[5] Pfeifer, Christian: Experimentelle Untersuchungen von Einflußfaktoren auf die Selbstzündung von gasförmigen und flüssigen Brennstofffreistrahlen. Zugl.: Karlsruhe, Inst. für Technologie, Diss., 2010, Karlsruhe, KIT Scientific Publ, 2010 (KIT scientific reports 7555).
[6] Gesellschaft Verfahrenstechnik und Chemieingenieurwesen: VDI-Wärmeatlas: Mit 320 Tabellen, 11., bearb. und erw. Aufl., Berlin, Springer Vieweg, 2013.
[7] Geilert, P.; Kolkwitz, B.; Eckebrecht, J.; Heinzel, C.: Einfluss der Kühlschmierstoffzufuhrbedingung auf die Energieeffizienz und die Leistungsfähigkeit von Schleifprozessen, 2016.
Products relevant to this article:
You may also be interested in these articles from our magazine:
Cooling lubricant and its relevance in grinding processes
Cooling lubricant is particularly relevant in the grinding process. But why grinding in particular? And what happens if the cooling lubricant is not used correctly? We answer these questions in this article.
Types of cooling lubricants
In addition to emulsions of different concentrations, in which various additives are used, the use of grinding oils is also common. We have compiled the areas of application, advantages and disadvantages, as well as the most important selection criteria for cooling lubricants for you.
Printed cooling lubricant nozzles
Team Grindaix also successfully uses 3D printing to manufacture flow-optimized cooling lubricant nozzles. We have summarized for you which aspects we were able to significantly improve and where the design and production challenges lay.
Cooling lubricant nozzles
Cooling lubricant nozzles generate the necessary outlet speed of the coolant. However, nozzles are not only required for cooling applications. You can find an overview of all applications and designs here.