Interferences on the cooling lubricant supply during grinding
The aim of a cooling lubricant supply that meets requirements is to achieve component machining that is free from thermal damage in order to achieve the highest form and dimensional tolerances in the shortest possible machining time. The grinding process involves various disturbances that can negatively affect a cooling lubricant supply that meets requirements. These are listed and briefly explained in this magazine article by Team grindaix.
In terms of possible disturbances, we basically distinguish between influences from the areas of:
a) Process control of the grinding process
b) Process control of the dressing process
c) Materials technology
d) Coolant (oil, emulsion, aqueous solution)
e) Coolant system
f) Coolant nozzle
g) The air cushion rotating with the grinding wheel
a) Process control of the grinding process
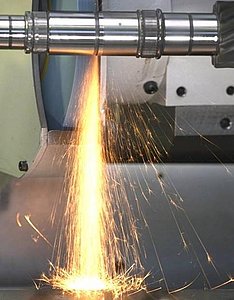
In the grinding process, the feed or, rather, the related time-based metal removal rate Q'w can be selected so improperly that the chip thicknesses (lengths) of the grinding chips become so large that they clog the pore spaces near the surface of the grinding wheel bond. This means that the accessible pore spaces are virtually smeared with soft component material (hot chips).
The result is that these pore spaces are no longer available for the transport of cooling lubricant to the machining zone. This means that, in theory, no cooling lubricant reaches the actual chip formation process and the cooling and lubricating effect of the cooling lubricant is lost. The component overheats.
A second effect of such grinding tool bonding clogging is the increasing friction between the grinding tool (bond) and the component during the grinding process. This also results in thermal influences that can negatively affect the surface zone properties of the component to be ground.
b) Process control of the dressing process
If the grinding tool is improperly dressed (too finely) with respect to the selected grinding process setting (Q'w), the friction between the grinding wheel and the component will be too high. On the one hand, we need a sufficiently rough grinding tool to be able to achieve high material removal rates. On the other hand, the grinding wheel should not be dressed too roughly so that the required surface quality can be achieved. Therefore, a compromise should be sought between a grinding tool that is as easy to cut as possible and a sufficiently fine component surface that can still be achieved. The choice of dressing parameters has a significant influence on the surface topography of a grinding wheel.
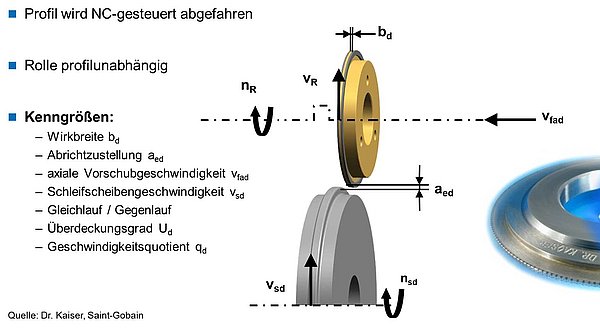
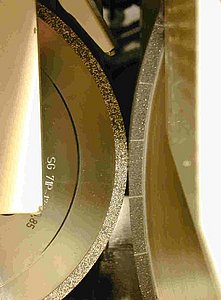
The terms commonly used here, such as the dressing overlap Ud, the dressing speed ratio qd, the effective width of the dressing tool bd, the dressing infeed aed and the feed rate in the dressing process, are decisive factors influencing the subsequent thermal damage to the surface zone of the component. Even the most professionally designed cooling lubricant feed is virtually ineffective if the pore spaces in the grinding tool cannot be used to transport the cooling lubricant as required. The grinding tool is the coolant carrier. If the pore spaces are too small in relation to the chip sizes produced in the grinding process, as a result of an incorrectly designed dressing process, the grinding tool surface will become clogged, as described above. The result is grinding burn.
c) Materials technology
The material to be processed usually cannot be varied and is a customer requirement. However, if you understand which material components are present, you can derive specific information about the potential for grinding burn.
A distinction is made between hardened and unhardened material. The term “hardening” refers to the heat treatment of the component material to be machined. This gives the component targeted surface zone properties that make it robust against mechanical and chemical stresses during its subsequent use (intended purpose) and suitable for subsequent precision machining. Soft structural components of the materials to be processed lead to clogging of the pore spaces of the grinding tool during the grinding process. These are then no longer available for the necessary transport of cooling lubricant to the grinding zone. Hard structural components are desirable because they produce short chips and thus reduce the tendency to clog.
Which structural components have which influence on the addition in which form is discussed in detail in the seminar “Avoiding Grinding Burn”, not only for steels, but also for high-temperature materials such as titanium and nickel-based alloys, as well as for ultra-hard materials such as ceramics, hard metals and high-speed and tool steels.
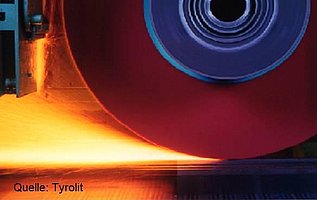
d) Coolant
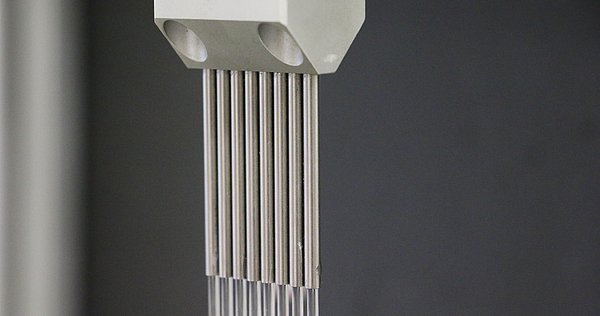
The type and composition of a cooling lubricant also has a decisive influence on grinding without thermal damage. Emulsions are usually mixtures of mineral oil (approx. 4-9%) and water (91-96%). Due to the relatively high water content, they have a very good cooling effect, but they also tend to foam. A heavily foaming emulsion causes the water content of the cooling lubricant supplied to the process via the free pore spaces of an abrasive wheel to drop sharply. This reduces the cooling capacity, which in turn can lead to thermal damage to the component. The heat has no choice but to either remain in the grinding tool, be absorbed into the cooling lubricant or migrate into the component.
The latter effect is not desirable. Abrasive discs are usually ceramic or resin-bonded. These materials are less likely to dissipate heat. Therefore, the aim must be to dissipate the heat generated during the grinding process via the cooling lubricant. The low biological resistance of an emulsion can lead to the formation of fungi, which in turn can lead to deposits in cooling lubricant pipes and cooling lubricant nozzles. In extreme cases, this can lead to blockages in the nozzles and pipes. Therefore, cooling lubricant nozzles that are operated with emulsion must be cleaned automatically at discrete time intervals as required. Furthermore, it is difficult to accelerate a foamy emulsion through pressurized cooling lubricant nozzles in such a way that it has a sufficiently high kinetic energy to penetrate the air cushion rotating with the grinding wheel. In most cases, foaming emulsions only come into the vicinity of the machining zone if they are applied improperly and therefore do not contribute to cooling the grinding process as required. Oils, on the other hand, have a lower heat absorption capacity than water, but they lubricate the chip formation process in such a way that less frictional heat is generated.
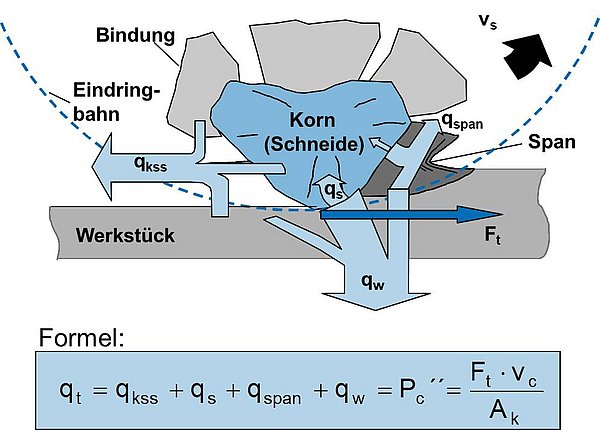
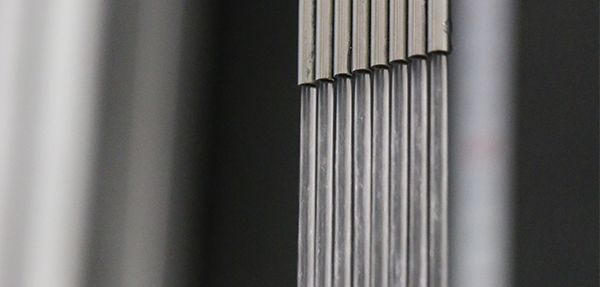
These two contrary effects (emulsion cools better but lubricates poorly; oil lubricates very well but cools less well) usually cancel each other out, and a general preference for one or other type of coolant cannot be made without considering other aspects (cost-effectiveness, environmental regulations, human compatibility). Oils exhibit a viscosity-temperature behavior. This must be taken into account when speaking of exact cooling lubricant feed quantities in grinding processes. Likewise, oils can exhibit foaming behavior. One then speaks of an air content of the oil (in %). Here, too, undesirable effects occur with regard to the reducing lubricating effect of an oil with a high air content. It should be mentioned here that aqueous solutions behave very similarly to emulsions in terms of their heat absorption capacity.
e) Coolant system
Errors can also occur in the design of the cooling lubricant system technology, which can cause thermal damage to components that are to be ground. In the context of this magazine article, a cooling lubricant system includes all installed mechanical units that come into direct contact with the cooling lubricant of a production unit. These include pumps, valves, pipes, cooling lubricant filtration systems, protective filtration systems, cooling lubricant cooling units, machine extraction systems and machine bed flushing systems. The cooling lubricant nozzles also come into contact with the cooling lubricant, but we will deal with this topic separately below.
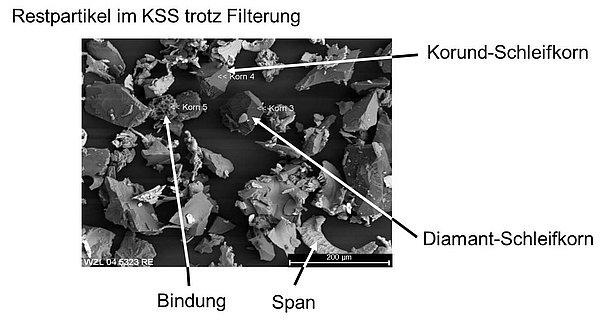
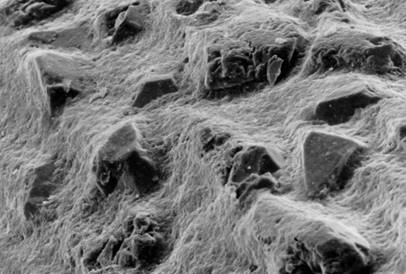
In the event of a fault in the cooling lubricant system, the proper supply of the cooling lubricant to the processing site with regard to the required quantity, the chemical and/or physical condition, can be affected to such an extent that the components are thermally damaged by the grinding process. In particular, increasingly clogged pipelines due to excessive cooling lubricant contamination can cause a pressure drop downstream of the blockage, resulting in an undersupply to the connected cooling lubricant supply systems. The cooling lubricant exit speed decreases and thus the cooling lubricant jet cannot penetrate the air cushion rotating with the grinding wheel as required. The cooling lubricant does not enter the pore space of the grinding wheel bond and is thus not supplied to the machining point. The temperatures during chip formation thus reach values that lead to a lasting increase in tensile residual stress in the component surface zone. Such pressure drops can also result from the mechanical wear of the units installed in the cooling lubricant system, such as pumps and valves. If the cooling lubricant cooling system fails or its performance is impaired for a variety of reasons, the temperature of the cooling lubricant will rise and the heat absorption capacity of the cooling lubricant in the machining process will decrease.
f) Coolant nozzle
A significant effect on the supply of cooling lubricant in line with requirements is the interference resulting from the design of a cooling lubricant nozzle. A suitable nozzle supplies the cooling lubricant to the cutting point at all times during grinding. This can be done directly by directing the jet of coolant onto the machining point, or indirectly by supplying the coolant to the free pore spaces of the grinding wheel. In both cases, the jet of coolant must penetrate the air cushion rotating with the grinding wheel and, after penetration, must exhibit a sufficiently high jet quality at a sufficient coolant speed. The lubricoolant exit speed is directly dependent on the grinding wheel peripheral speed and results from the lubricoolant pressure, which must be adjusted to the grinding wheel peripheral speed and applied to the nozzle.
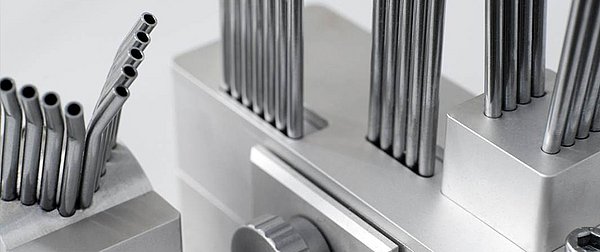

Taking into account the nozzle cross-section, the amount of cooling lubricant flowing through the nozzle is also calculated. It is easy to see that a large nozzle cross-section leads to a low cooling lubricant exit speed and also to high cooling lubricant volume flows. Both should be avoided if possible. The jet of cooling lubricant should be directed as compactly as possible to the machining point and/or the grinding wheel topography. Finally, high quantities of cooling lubricant also require a correspondingly large cooling lubricant filtration system. If the required cooling lubricant purity is not maintained, a nozzle outlet opening that is too small can lead to nozzle clogging. In general, it is therefore quite complicated to determine a nozzle technology that meets the requirements.
The team at Grindaix is always available to provide professional advice on all technical matters relating to the design of your cooling lubricant system, your dressing process, your grinding method, your choice of grinding media and the design of cooling lubricant nozzles. We look forward to hearing from you.
g) The air cushion
The grinding wheel as a tool is a rotating body that allows an air cushion to form due to the porosity of its surface. In terms of physics, the phenomenon of boundary layer adhesion occurs here. The relative speed between the boundary layer near the disc and the grinding disc is therefore zero. Using the Navier-Stokes equations, it can be analytically determined that the speed of the air cushion, directly on the grinding disc surface, consequently corresponds to the circumferential speed of the grinding disc and thus to the cutting speed vc . This is due to the friction between the surrounding air and the grinding wheel surface. As the distance from the wheel surface increases, the flow velocity of the air cushion decreases.
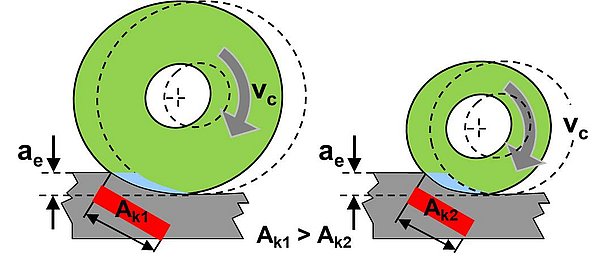
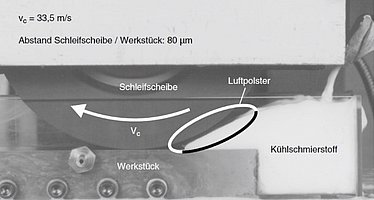
Since grinding wheels are usually ceramic-bonded, they have a high surface roughness over their entire surface. Therefore, there is a boundary layer adhesion of the ambient air over the entire surface of the grinding wheel, resulting in a centrifugal pump effect caused by the rotation. Ambient air is drawn in laterally by the rotating grinding wheel and discharged again in a radial direction over the outer surfaces. The air cushion can be made visible by means of simple experiments. Figure 9 shows an experimental set-up for making the grinding wheel air cushion visible during surface grinding.
The centrifugal pumping effect and the rotation of the grinding wheel create a characteristic flow direction of the air cushion, which can be broken down into different force components using a vector decomposition. Figure 10 schematically shows the force components based on a freely rotating grinding wheel. The lateral inflow of air at the flank of the grinding wheel and the subsequent discharge to the circumferential tool surface can be clearly seen. The x- and y-components are to be mentioned here as significant force components that lead to a deflection of the coolant jet. In the direction of rotation of the grinding wheel, or the vertical (y), a distance-dependent flow velocity and the flow forces dependent on it can be observed. Likewise, a variance in flow velocity occurs across the width of the grinding wheel and depending on the radial distance from the wheel surface. The air cushion therefore has a certain morphology with regard to the flow velocities that occur, which depend on the type of grinding wheel used, but also on the circumferential speed vc.
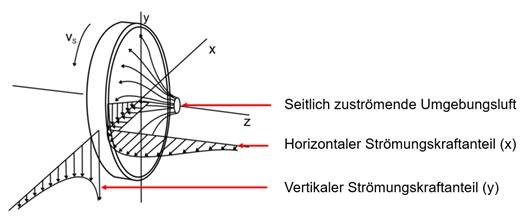
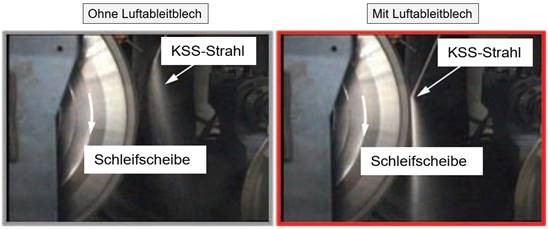
The deflection effects of the cooling lubricant jet by the air cushion can be demonstrated by means of experiments. Figure 6 shows a comparison of two cooling lubricant supply conditions, in which the influence of the air cushion is observed with and without an air discharge device.
In this test, a deflector plate for the air cushion is installed as a comparison to the non-deflected air cushion, with the same cutting and cooling lubricant supply parameters. It can be clearly seen that the jet force of the cooling lubricant nozzle alone is not sufficient to penetrate the air cushion at the selected supply parameters. Under these circumstances, the grinding gap, as the contact point between the grinding wheel and the workpiece, would not be sufficiently supplied with cooling lubricant without the additional use of a deflection plate.
This and other experiments show that the air cushion does in fact influence the cooling lubricant supply. However, Heinzel describes various contrary assessments of the influence of the air cushion on the cooling lubricant supply, based on different cooling lubricant nozzle designs. [3]
- The influence of the air cushion is said to be controversial and to play a subordinate role.
- At high cutting speeds (vc ≤ 130 m/s), the disruptive influence increases.
- With point jet nozzles, no disruption of the jet is to be expected due to the high jet velocity.
Regardless of the assessments mentioned, however, the observed disruptive influence of the air cushion is decisive for countermeasures to weaken or penetrate the air cushion. Due to the many variable process parameters, starting with the grinding wheel used, the machining process or the cutting speed, there are also variable forms of the air cushion with different disruptive influences on the cooling lubricant jet.
[1] [Beck Thorsten, Berichte aus der Produktionstechnik, Kühlschmierstoffeinsatz beim Schleifen mit CBN, Aachen, Shaker Verlag, 2001, Band 28/2001]
[2] [T.Yoshimi, S.Oishi, S.Okubo, H.Morita. Development of Minimized Coolant Supply Technology in Grinding. JTEKT Engineering Journal English, 2010]
[3] [Heinzel Dipl.-Ing. Carsten; Methoden zur Untersuchung und Optimierung der Kühlschmierung; Bremen; Universität Bremen; 1999]
Do you have any further questions?
We are always happy to answer any questions you may have about our products and services. You can contact us by email at info@grindaix.de or by phone at +49 (0)2273 95373 0 (weekdays from 8 a.m. to 4.30 p.m.).
Products relevant to this article:
You may also be interested in these articles from our magazine:
Cooling lubricant nozzles
Cooling lubricant nozzles generate the necessary outlet speed of the coolant. However, nozzles are not only required for cooling applications. You can find an overview of all applications and designs here.
Options for influencing the air cushion
Various standard practical solutions are used to overcome the air cushion. The aim in all cases is to mitigate or completely avoid the negative influence of the air cushion on the cooling lubricant jet.
Fluidic consideration of the air cushion
Based on the phenomenon of boundary layer adhesion described above, additional studies on the shape and characteristics of the grinding wheel air cushion are available in the literature.
Types of cooling lubricants
In addition to emulsions of different concentrations, in which various additives are used, the use of grinding oils is also common. We have compiled the areas of application, advantages and disadvantages, as well as the most important selection criteria for cooling lubricants for you.