Verfahren der Schleifbrandprüfung
Während des Schleifprozesses tritt oftmals eine thermische Schädigung, Schleifbrand, am Bauteil auf. Verursacht wird Schleifbrand durch einen zu großen Temperatureintrag. Die Folge sind ein Qualitätsverlust und hohe Kosten, wenn beispielsweise Bauteile aussortiert werden müssen.
Zur Wahrung und Verhinderung dieser Aspekte, ist also eine Überprüfung geschliffener Bauteile im Rahmen der Qualitätskontrolle unerlässlich. Nicht selten ist Schleifbrand an einem geschliffenen Bauteil mit bloßem Auge nicht zu erkennen. Daher haben sich verschiedene Schleifbrand-Prüfverfahren etabliert, die eine zuverlässige Schleifbranderkennung umsetzbar machen.
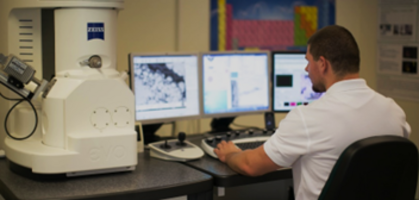
Zerstörungsfreie und zerstörende Verfahren – der Unterschied
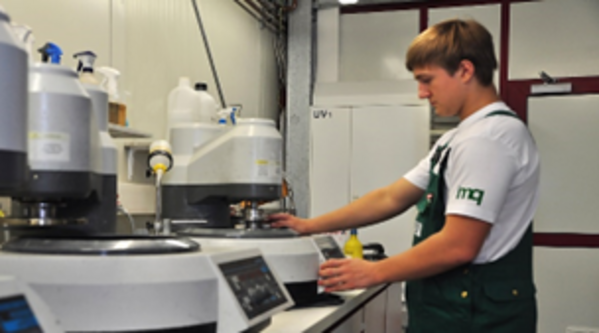
Schleifbrand-Prüfverfahren helfen sicherzustellen, dass nur Bauteile ohne Schleifbrand den Fertigungsbetrieb verlassen. Die Schleifbrandprüfung wird dabei grundsätzlich in zwei wesentliche Bereiche untergliedern, den zerstörungsfreien und den zerstörenden Verfahren.
Bei der zerstörungsfreien Schleifbrandprüfung, beleibt das gefertigte Bauteil während und nach der Prüfung intakt. Mit diesen Prüfmethoden ist eine vollständige Qualitätssicherung ohne Verlust von Bauteilen durch Zerstörung möglich. Zu zerstörungsfreien Schleifbrandprüfung zählen unteranderem das Barkhausenrauschen oder die Nitalätzung.
Die zerstörende Schleifbrandprüfung beschreibt eine Analyse, bei der das Bauteil zerstört werden muss. Eine zerstörende Schleifbrandprüfung ist genau und eindeutig, allerdings ungeeignet, um kosteneffizient im Serienbetrieb die Schleifbranderkennung sicherzustellen. Somit sind diese Prüfverfahren, also nur im Einzelfall anwendbar.
Zerstörungsfreie Prüfverfahren
Zu den bekanntesten zerstörungsfreien Prüfverfahren für Schleifbrand, zählen das Barkhausen-Rauschen und das Nitalätzen. Das Barkhausen-Rauschen ist ein magnetinduktives Verfahren und das Nitalätzen ist eine chemische Methode, weshalb beide Verfahren sich grundsätzlich vom Aufbau voneinander unterscheiden.
Das Barkhausen-Rauschen
Beim Barkhausen-Rauschen werden die elektromagnetischen Eigenschaften metallischer Werkstoffe genutzt, um Schleifbrand zu erkennen. Es wird der Verlauf sogenannter Hystereschleife, oder auftretender Amplituden, mit einer Differenzsonde im Bauteil erzeugt. Diese wird im selben Arbeitsgang gemessen. Grundsätzlich zeigen hierbei große gemessene Amplituden Zugspannungen im Bauteil an. Kleine Amplituden hingegen zeigen Druckspannungen an. Die erhobenen Messwerte müssen anschließend auf die Amplituden eines vorab gemessenen, schleifbrandfreien Bauteils bezogen werden. Dieses Referenzbauteil muss von seinen Eigenschaften dem gemessenen Bauteil ähneln. Auf dieser Grundlage wird ein Toleranzband festgelegt. Liegen die gemessenen Amplituden innerhalb dieses Toleranzbandes wird das Bauteil als schleifbrandfrei erkannt. Amplituden ober- bzw. unterhalb der Toleranzgrenze, haben Schleifbrand.
Übersicht zum Barkhausen-Rauschen:
- Magnetinduktiv
- Amplitudenmessung
- schleifbrandfreies Bauteil nötig
- flexibel
- kurzfristig einsetzbar
- Chargeneinfluss möglich
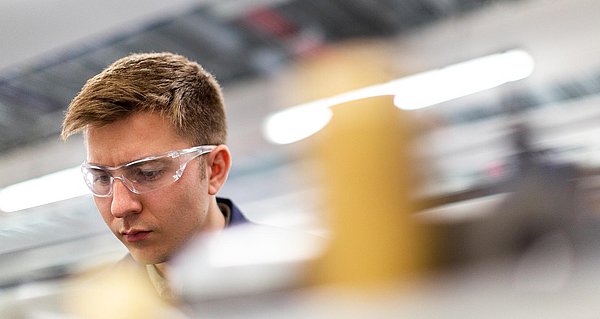
Das Barkhausen-Verfahren ist sehr flexibel und im Bedarfsfall auch kurzfristig zwischen den einzelnen Bearbeitungsschritten einsetzbar. Zudem ist die Schleifbrandprüfung ohne subjektive Einflüsse des Prüfers durchführbar. Nachteil des Barkhausen-Verfahrens ist jedoch der Chargeneinfluss auf die Messergebnisse. Da sich die Chargen des verwendeten Werkstoffes oftmals nicht gleichen, kann sich die Gültigkeit der Referenzmessung ändern. So kann es dazu kommen, dass auch schleifbrandfreie Bauteile als Ausschuss deklariert werden. Ebenso kann es passieren, dass Schleifbrandzonen nicht zuverlässig detektiert werden können, da sich die Amplituden überlagern und Schleifbrand folglich nicht erkannt wird.
Das Nitalätzen
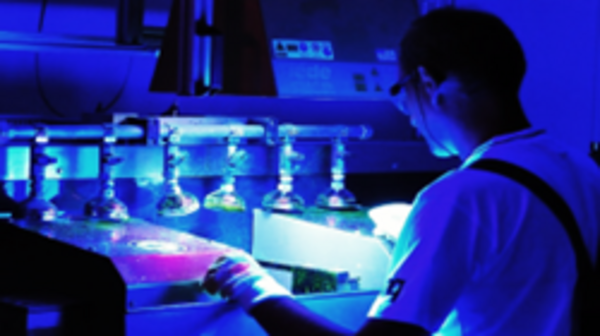
Bei dem Nitalätzen handelt es sich um eine chemische Prüfmethode, um den Schleifbrand zu identifizieren. Dabei wird das Bauteil in ein Bad, meist aus Salpetersäure (HNO3) getaucht, abgespült und anschließend optisch auf Verfärbungen der Oberfläche hin untersucht. Bei Bauteilen, welche Schleifbrand aufweisen verfärbt sich die Oberfläche (Kohlenstoff) infolge einer Reaktion mit der Säure in verschiedenen Graustufen. Diese machen die Intensität des Schleifbrandeinflusses sichtbar. Im Nachhinein kann das Bauteil anhand einer optischen Grauskala manuell bewertet werden. Das Durchlaufverfahren kann sowohl automatisch als auch manuell erfolgen. Das Nitalätzen ist das bisher einzige international genormte Schleifbrand-Prüfverfahren und bei allen Bauteil-Geometrien einsetzbar. Allerdings unterliegt es einem großen subjektiven Einfluss durch den Prüfer, der die optische Bewertung durchführt. Aus diesem Grund muss das Personal für das Nitalätzen speziell geschult werden. Weiterhin werden hohe Anforderungen an Arbeits- und Umweltschutz im Umgang mit der notwendigen Säure gestellt. Das Nitalätzen hat je nach Bauteil einen höheren Zeitaufwand bei der Schleifbrandprüfung zur Folge. Bei unsachgemäß angesetzten Säurebädern kann es allerdings zu fehlerhaften Messungen kommen.
Zerstörende Prüfverfahren
Bei den zerstörenden Prüfverfahren ist das Bauteil nach der Prüfung nicht mehr einsetzbar, weshalb es nur in Einzelfällen und stichprobenartig eingesetzt wird. Jedoch gehören diese Prüfverfahren zu den genausten und eindeutigsten, um Schleifbrand festzustellen. Eines dieser Verfahren ist die Mikrohärteprüfung.
Die Mikrohärteprüfung
Die Mikrohärteprüfung ist neben der Identifizierung von Mängeln, wie Schleifbrand, auch für die Bewertung von mechanischen oder Materialeigenschaften wichtig. Zur Werkstückprüfung mithilfe der Mikrohärteprüfung muss das Bauteil zerstört werden, indem ein Gefügeschliff durch das Bauteil als Prüffläche genutzt wird. Auf der vorbereiteten Prüffläche werden mehrere Härteprüfungen mit dem Prüfverfahren nach Vickers (HV) durchgeführt.
Anhand der gemessenen Härten und der Verteilung der auftretenden Härtegrade kann sicher bestimmt werden, ob am untersuchten Bauteil Schleifbrand vorliegt. Die Mikrohärteprüfung ist allerdings ein aufwendiges Verfahren, da es aus mehreren einzelnen Hartmessungen besteht. Die Auswertung, Zerstörung des Bauteils und Vorbereitung erfordern zusätzlich Zeit und Kosten an Personal und Material.
Vorteile der Mikrohärteprüfung:
- Identifizierung von Versagen (Schleifbrand)
- Eigenschaften bewerten
- Eindeutig, zuverlässig und genau
Nachteile der Mikrohärteprüfung:
- Bauteilzerstörung
- Aufwendig
- Zeit- und Kostenintensiv
Alle Prüfverfahren auf einen Blick
Übersichtlich: Alle oben genannten Prüfverfahren und viele mehr, fassen wir für Sie hier mit ihren Abkürzungen und dem Prinzip des Verfahrens kurz zusammen.
Zerstörungsfreie Prüfverfahren:
Verfahren | Abkürzung | Prinzip |
Nitalätzung | STE | chemisch |
Barkhausenrauschen | BHR | magnetinduktiv |
Oberflächenrissprüfung | PT | / |
Ultraschallprüfung | UT | mechanisch |
Wirbelstromprüfung | ET | elektrisch |
Zerstörende Prüfverfahren:
Verfahren | Abkürzung | Prinzip |
Mikrohärteprüfung nach Vickers | MHV | mechanisch |
Rasterelektronenmikroskop-Aufnahme | REM | elektronenstrahl |
… |
Ihre Fragen – Unsere Antworten
Welche Schleifbandprüfung ist am nützlichsten?
Ein Urteil über die Nützlichkeit lässt sich nicht pauschal treffen. Hier muss jeder Fertigungsbetrieb selber entscheiden. Grundsätzlich kann man sagen, dass die zerstörenden Prüfverfahren genauer sind, allerdings geht diese nicht ohne die Zerstörung des Bauteils. Dadurch entsteht, ein gewisser Ausschuss und somit steigende Kosten. Die zerstörungsfreien Prüfverfahren hingegen reduzieren den Ausschuss durch zerstörte Werkstücke, sind aber auch weniger genau, weshalb Schleifbrand auch mal unentdeckt bleiben kann.
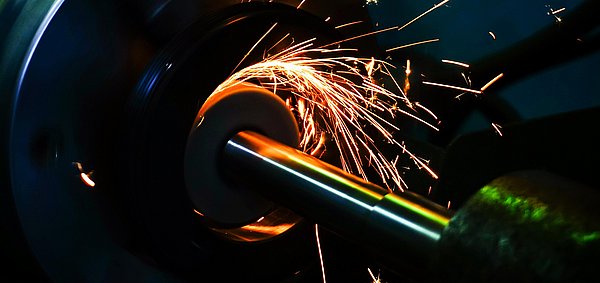
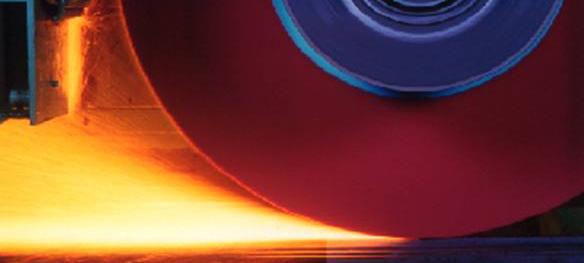
Ist eine aufwendige Schleifbrand-Prüfung nötig?
Schleifbrand ohne ein Prüfverfahren zu erkennen ist herausfordernd. Ein Schleifbrand-Prüfverfahren zu nutzen ist sinnvoller, da auch wenn die Beschaffung des nötigen Materials und die Durchführungen sowohl zeit- also auch kostenintensiv sein können, die Gefahr von Schleifbrand größer ist. Wenn Schleifbrand unerkannt bleibt und zum Kunden verschickt wird, kommt es höchstwahrscheinlich zu einer noch zeit- und kostenintensiveren Reklamation.
In diesem Artikel relevante Produkte:
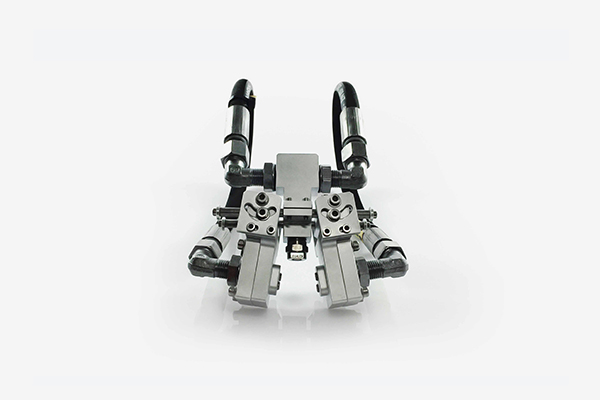
Diese Artikel aus unserem Magazin könnten Sie auch interessieren:
Schleifbrand
Thermische Randzonenschädigung durch Gefügeänderung – gemeinhin als Schleifbrand bekannt. Wir erläutern den werkstofftechnischen Hintergrund und geben erste Ansätze für die Schleifbrandvermeidung.
Schleifbrandprobleme lösen
Ein Schelfibrandproblem lösen? Das ist leichter gesagt als getan! Wir haben einige Lösungsstrategien erarbeiten und in unserem Magazinbeitrag zum Thema "Schleifbrandprobleme lösen" für Sie zusammengefasst.
Schleiftechnik
Einen Überblick über das komplexe Thema Schleiftechnik mit seinen vielfältigen Einflussgrößen geben wir in unserem Artikel „Schleiftechnik“. Hier bieten wir Ihnen eine vollständige Übersicht über alle relevanten Parameter.
Schleifprozess richtig kühlen
Den Schleifprozess richtig kühlen! Das ist einfacher gesagt als getan. Was man hierzu an verschiedensten Parametern beachten muss und welche Versorgungs-Lösungen geeignet oder ungeeignet sind, haben wir hier zusammengestellt.