Cooling lubricant nozzles - Defined lubricoolant supply for optimum process flow
Machine tools are ultra-modern machining centers for metalworking in which a wide variety of components and systems work together. Each of these subsystems contributes to the accuracy, reliability, efficiency and service life of the entire machine tool. The cooling lubricant supply is also an essential component of an efficiently operating machine tool. In our article “Coolant nozzles for machine tools”, we take a closer look at this component of the cooling lubricant system.
Tasks of cooling lubricant nozzles
The task of a coolant nozzle seems trivial at first, as it directs the coolant to the cutting point where it is needed. However, in addition to the targeted supply of coolant, the nozzles also perform a wide range of other tasks that have made coolant nozzles highly technical components of the coolant system and contribute significantly to process reliability and efficiency. Depending on the application and processing task, lubricoolant nozzles perform the following tasks
- Process cooling: Reduction of heat generation in the chip formation process by reducing the friction power (lubrication effect) and absorbing the process heat (cooling effect), which prevents overall thermal damage (e.g. grinding burn).
- Cleaning: Removal of machining residues from the pores of the grinding wheel bond to ensure cutting capability and sufficient lubricoolant absorption through the free pores of the grinding wheel bond.
- Saturation: Filling the free grinding wheel pores with cooling lubricant for process cooling of hard-to-reach machining zones.
- Extinguishing: Extinguishing the “spark jet” (glowing chip particles behind the grinding zone) to reduce the risk of oil-aerosol deflagrations (only with oil) and minimize wear of the affected machine components and machine contamination (with oil and emulsion).
- Flushing: Flushing the machine bed with cooling lubricant to remove machining residues from the machining area of the machine. This reduces the amount of manual cleaning required.
Requirements for lubricoolant nozzles
Cooling lubricant nozzles accomplish these tasks exclusively through the use of cooling lubricant, which is supplied at a certain pressure and volume flow by a cooling lubricant filter system. The task of the cooling lubricant nozzle is then to generate suitable jet patterns (nozzle effectiveness) at the lowest possible cooling lubricant volume flows (nozzle efficiency), depending on the intended use. Challenges in the implementation of cooling lubricant nozzles Cooling lubricant nozzles are precisely adapted to their intended use, which results in a wide variety of products. One of the main challenges when designing coolant nozzles is to ensure that the machining zone is supplied as completely as possible. This must be reliably supplied with sufficient lubricoolant over the entire area. Adapting the nozzle to the contours of the component ensures that the machining zone is supplied with lubricoolant in a targeted manner at every point. However, it is not sufficient to only supply the cooling lubricant to the machining zone.
The coolant supply must occur at a certain speed, which is usually present at the nozzle as the coolant exit speed. The exit speed of the coolant from the nozzle must be high enough to ensure that, despite all the losses along the spray path, a sufficiently high spray speed is still present at the machining zone. The geometry of the nozzle, as well as the applied pressure and volume flow, determine the exit speed through the nozzle. The coolant jet should travel as laminarly as possible between the nozzle and the machining zone, since a turbulent jet is not targeted and is subject to large flow losses. If the speed of the coolant jet is sufficiently high, it can penetrate an air cushion rotating with the grinding wheel. The coolant reaches the machining zone and is not deflected from it. The coolant nozzle is also responsible for ensuring that the coolant flows as laminarly as possible.
Types of cooling lubricant nozzles
There are various ways to supply cooling lubricant. In addition to DIY solutions, these include high-tech products that significantly improve the cooling lubricant supply. Some designs are briefly presented below:
- Self-made: A more elaborate form of the KSS nozzles are welded or bolted self-made nozzles made of several components, often designed as slot nozzles. Although this design already generates a significantly better KSS supply than would be the case with simple open pipe ends, high flow losses often occur due to unfavorable component design. In addition, the user has no knowledge of the nozzle's characteristic values, making it almost impossible to adjust the nozzle correctly to the grinding process using the pressure and volume flow of the supplied cooling lubricant.
- Needle nozzles: Needle nozzles are an established design of cooling lubricant nozzle for machine tools and ensure a very targeted and, above all, laminar supply of the cooling lubricant to the cutting point. It is also possible to adapt the nozzle geometry to the component contour. However, the many small nozzle tubes cause relatively high flow losses, which have to be overcome by a correspondingly increased supply pressure of the cooling lubricant.
- Tubes: A simple do-it-yourself solution is to use tubes with a cross-section reduction on the outlet side, which generates an increase in the outlet speed. However, the cheap and easy implementation is counteracted by imprecise cooling with an often much too high cooling lubricant volume flow.
- 3D-printed nozzles: Recently, 3D-printed nozzles have been used more and more. These enable flow optimizations, weight reductions and complex installation space restrictions that could not previously be economically produced using conventional manufacturing processes. Further information on 3D-printed cooling lubricant nozzles can be found on our product page, where we also have interesting product videos available for you.
Summary
Reliable process cooling is indispensable for a stable and economical manufacturing process. It is particularly important that a cooling lubricant reaches the cutting point in a targeted manner and with a coordinated volume flow and sufficient speed. The CL nozzle is responsible for this. It can be realized in different versions and designs and can perform a wide range of tasks within the machine tool. In addition to low-cost self-made devices, specially designed cooling lubricant nozzles are also available that enable a noticeable improvement in the cooling lubricant supply situation. The supply of the cooling lubricant nozzles in a machine tool is not trivial, since it must be ensured for every production scenario that the process supply is sufficiently high, the cleaning does not damage the tool, the impregnation is not ineffective, the air cushion is always discharged and the machine interior is successfully cleaned. Since there is often only one central pressure before the machine, the pressure distribution must be coordinated with all the nozzles used in line with requirements. Otherwise, grinding burns will occur, resulting in rejects!
For this reason, Grindaix GmbH has been developing and selling cooling lubricant nozzles for years that supply the necessary cooling lubricant to the machining tasks noticeably more reliably and effectively. For this purpose, we offer an extensive portfolio of nozzles in a wide range of designs for a wide range of tasks within the machine tool. The coolant nozzles are complemented by our extensive measuring and control accessories, which, in combination with the individual characteristic curve of each nozzle, allow the nozzle to be precisely matched to the machining process. To bring your coolant supply up to date, contact the coolant specialists at Grindaix.
Products relevant to this article:
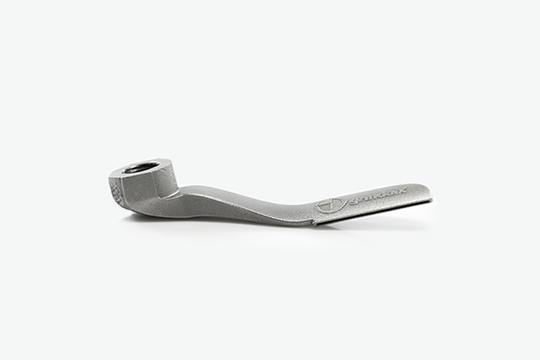
You may also be interested in these articles from our magazine:
Cool the grinding process properly
Cool the grinding process properly! This is easier said than done. We have compiled a list of the various parameters that need to be taken into account and which supply solutions are suitable or unsuitable here.
Cooling lubricant supply
It is easy to understand that grinding processes need to be supplied with cooling lubricant. But what exactly does the cooling lubricant do and what are the challenges involved in supplying cooling lubricant?
Types of cooling lubricants
In addition to emulsions of different concentrations, in which various additives are used, the use of grinding oils is also common. We have compiled the areas of application, advantages and disadvantages, as well as the most important selection criteria for cooling lubricants for you.
Cooling during grinding
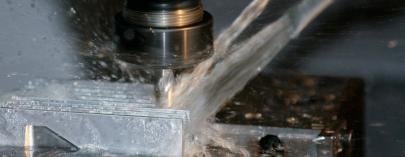
A great deal of heat is generated during grinding due to process-related friction. This heat must be reliably dissipated, which is why grinding processes require reliable cooling. You can read about what is important here.