Ressourcensparende KSS-Zufuhr beim Schleifen?
Nicht erst seit dem Russland-Ukraine-Krieg und den damit verbundenen steigenden Energiekosten wird sich intensiv mit der Frage beschäftigt, wie entlang der Prozesskette Einsparungen beim Energie- und Ressourcenverbrauch zu realisieren sind. Zusätzlich müssen sich Unternehmen damit auseinandersetzen, die CO2-Emissionen deutlich zu reduzieren und ressourcenschonend zu produzieren. In der aktuellen Zeit achten immer mehr Firmen auf ihren eigenen ökologischen Fußabdruck. Das Ziel: Bis 2030 soll die Treibhausemission im Vergleich zum Jahr 1990 um ganze 55 % reduziert werden. Fraglich ist nur, wie dies erreicht werden kann, ohne große Auswirkungen auf die Produktion zu haben.
Auf vielen nationalen und internationalen Kongressen und Tagungen wurde in der Vergangenheit genau dieses Thema zur Agenda gemacht. So beschäftigen sich Branchenexpertinnen und -experten mit der Frage, wie entlang der gesamten Prozesskette Einsparungen von Energie und Ressourcen vorgenommen werden können. Seit Jahren liegt der Fokus auf der ressourcenschonenden Produktion, vor allem aber auf die Einsparung von Ressourcen beim Schleifen.
Während in den 1990er-Jahren die Unternehmen das Problem ignorieren konnten, können die Unternehmen es heute nicht mehr tun. Die Regierung und auch die Kunden legen immer mehr Wert auf eine nachhaltige und ressourcensparenden Produktion. Die steigenden Energie- und Rohstoffpreise, gepaart mit den Erwartungen der Kunden und den gesetzlichen Bestimmungen durch die Regierung sorgen dafür, dass die Energieeffizienz gerade beim Schleifen kritisch hinterfragt wird.
Allerdings treffen hier bereits die ersten Unternehmen auf ein Problem. Ca. 80% der Unternehmen, die Schleifen als ein Fertigungsverfahren anbieten, kennen die anlagenspezifischen Betriebsmittelzustände und auf die Produktionsmaschinen bezogene Verbräuche nicht. Vielen ist dabei nicht bewusst, dass der KSS-Verbrauch (Kühlschmierstoffe) 60% des gesamten Energieverbrauchs der Maschine ausmachen. Teilweise ist den Unternehmen gar nicht bewusst, dass bis zu 50% an unnötigen KSS-Mengen in Bettspülung und in die Bauteilreinigung verschwenden. Auf der anderen Seite sind produktivitätsrelevanten Stellen häufig unterversorgt. Jedoch kann auch ein Überversorgung von KSS sich negativ auf den Schleifprozess auswirken. In der Industrie wird in einigen Fällen zu hoher Druck und vor allem hohe Menge an KSS eingesetzt. Diese Mengen können dabei gar nicht von der Kontaktzone zwischen Schleifscheibe und Werkstück aufgenommen werden. Folglich ist es schwer, an diese Stelle eine Optimierung bei der Einsparung von KSS vorzunehmen, da keine Daten gesammelt und somit nicht optimiert werden können.
Probleme beim Schleifen im Kontext der Ressourcenverschwendung
Schleifen ist ein Fertigungsverfahren, dass sich vor allem durch die hohen Maß- und Formgenauigkeit auszeichnet. Dabei ist es im Gegensatz zu anderen Fertigungsmethoden ein energieintensives Verfahren für vergleichsweise wenig Werkstoffvolumen mit hohem Aufwand. Im Vergleich zu anderen Fertigungsverfahren muss beim Schleifen eine bedeutend höhere spezifische Energie zur Zerspanung eines Werkstoffvolumens eingesetzt werden. So ist es wichtig, dass eine adäquate Schmierung und Kühlung gerade bei hohem Materialabtragraten zur Vermeidung unerwünschter Gefügeeigenschaften geschliffener Bauteile gewährleistet ist.
Ebenfalls haben viele Unternehmen auch das Problem, dass sie veraltete Maschinen haben. Dies muss sich nicht zwingend negativ auf die Energieeinsparung auswirken. Folglich würde die Instandhaltung oder ein Retrofitting der Maschine die Kosten reduzieren, die im Falle einer Neuanschaffung auftreten würden.
Nutzungsdauer von Schleifmaschinen erhöhen
Um die Langlebigkeit der Maschine zu erreichen, können verschiedene Lösungen in Anspruch genommen werden. Ein einfacher Weg für Unternehmen wäre die Abschaltung von Maschinen in bestimmten Zeiten. Sie könnten beispielsweise die Maschinen nur in bestimmten Schichten laufen lassen, um Energie und Ressourcen einzusparen. Dies könnte jedoch der Produktivität und Flexibilität des Unternehmens entgegenwirken. Klingt theoretisch einfach und logisch, ist aber in der Praxis schwer umsetzbar, da gerade die Fertigung von großen Stückzahlen nicht ermöglicht, die Maschinen vollständig anzuhalten.
Die Langlebigkeit der Produkte (Maschinen) ist ein wichtiger Punkt in der Ressourcenreduktion. Dies kann durch eine Überarbeitung der Maschinen ermöglicht werde und wird als „Retrofit“ bezeichnet. Das Wort setzt sich aus dem lateinischen Wort „retro“ für rückwärts und dem englischen „fit“ zusammen, welches mit dem Wort „passen“ übersetzt werden kann. Unter dem Begriff versteht man die nachträgliche Aufrüstung und Modernisierung der älteren Maschinen z.B. durch die Anbindung von digitalen Systemen.
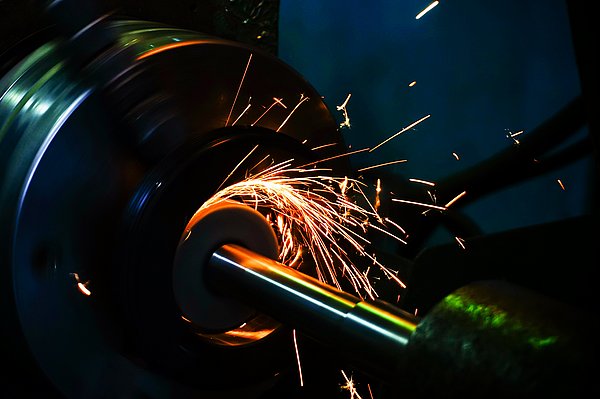
Optimierungsmöglichkeiten durch Retrofitting von Schleifmaschinen
Durch den Einbau von Sensoren können beispielsweise die Bearbeitungszeiten, die Auslastung der Maschine oder der Energieverbrauch identifiziert werden. Damit die Aufrüstung der Maschine durch den Einbau von Sensoren und optimierten KSS-Zufuhrsystemen sinnvoll ist, sollte, wie bereits oben erwähnt eine Analyse des „Istzustandes“ durchgeführt werden. Wenn diese Daten dann vorliegen, kann eine Strategie entwickelt werden, wo und welche Art der Aufrüstung an der Maschine umgesetzt werden soll. Diese gewonnenen Daten dienen zur Prozess- und Anlagenüberwachung und sorgt für eine verbesserte Qualitätssicherung und äußert sich in einer allgemeinen Prozessoptimierung.
Der Vorteil dabei ist, dass die vorhandenen Maschinen kostengünstig in ein digitales System eingebunden werden können. Dies wirkt sich positiv auf die Nutzungsdauer der Maschinen aus. Die Maschinen werden also in der Summe länger verwendet, was auch den Kosteneinsparungen des Unternehmens zugutekommt. Ebenfalls wird die Nachrüstung in das bestehende System integriert und somit der generelle Produktionsablauf nicht verändert. Des Weiteren wird durch das Retrofitting die Ausfallzeiten der Maschinen verringert, die Produktionskosten sind geringer, gesetzliche Vorgaben werden eingehalten und zuvor unbekannte Daten gesammelt. Diese ganzen Vorteile helfen den Maschinen, den Prozess zu optimieren, da die Aufrüstung an der richtigen Stelle eingesetzt werden kann, um das Maximale aus dem Prozess herauszuholen. So fallen keine hohen Investitionen bei der Neuanschaffung von Maschinen und auch keine zusätzliche Einarbeitung der Mitarbeiter an. Dies hat zur Folge, dass eine Ressourceneinsparungen an Geld und Zeit erreicht wird, die somit sinnvoll anderweitig verwendet werden können.
Durch das Retrofitting haben die Unternehmen die Möglichkeit, Maschinen- und Prozessdaten zu sammeln, die anschließend zu Steigerung der Energieeffizienz, der Qualität der Produkte sowie zu den Verbesserungen des gesamten Prozesses beitragen. So können auch die Steigerung des Produktionsvolumens und die Effizienz der Anlage einen möglichen Vorteil eines digitalen Retrofits sein. Aber nicht nur Prozesse können dadurch optimiert werden, sondern auch die KSS-Zufuhrsysteme können so angepasst werden. So kann die Einsparungen von viel Kühlschmierstoff verzeichnet werden und diese wirkt sich positiv auf die Ökobilanz des Unternehmens aus. Dies erhöht folglich auch die Produktivität der Maschinen. Durch die geregelte Zufuhr von Kühlschmierstoffen kann Schleifbrand vermieden und der Ausschuss reduziert werden. Dies spiegelt sich dann in der Qualität der Produkte wider. Des Weiteren kann durch diese Optimierung auch die Anzahl der Wartungen reduziert werden, was folglich reproduzierbare Ergebnisse ermöglichen und einen robusten Prozess schaffen.
Ressourcenschonung durch Digitalisierung
Die Digitalisierung ermöglicht den Unternehmen, den Verbrauch von Ressourcen maßgeblich zu reduzieren. Es hilft den Betrieben, die Prozesse zu optimieren und dabei den Energieaufwand gering zu halten. Die Daten beim KSS-Verbrauch werden statistisch ausgewertet und somit die wirklichen Verbrauchsdaten und bauteilbezogene Leistungsindikatoren identifiziert. Dieser digitale Assistent trägt dazu bei, dass der Verbrauch an Betriebsstoffen reduziert und grundsätzlich in allen Schleifmaschinen angewendet werden kann. Wenn die Betriebsstoffe nämlich in einer konstanten Qualität (physikalischen und chemischen Zuständen) mit einer bedarfsgerechten Menge zu jeder Zeit anforderungsgerecht den Produktionsmittel zugeführt werden, kann dies zu enormen Einsparungen von Ressourcen führen.
Warum ist Ressourcenschonung in der Produktion wichtig?
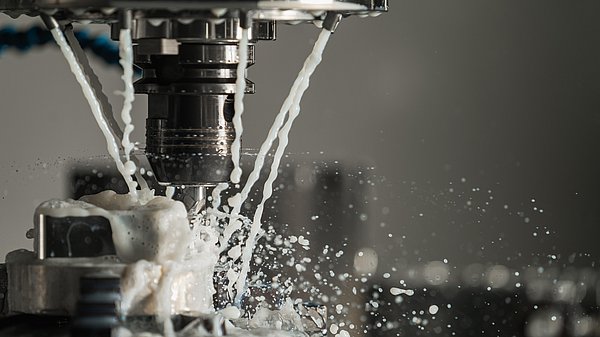
Gerade in Zeiten, wo Energiepreise steigen, müssen viele Produzenten die Kosten auf die Kunden abwälzen. Zusätzlich dazu werden auch die gesetzlichen Vorgaben immer strenger, was die Unternehmen zwingt, ihre Produktion zu hinterfragen.
Die Aufgabe der Werkzeugindustrie ist, die Nachhaltigkeit und Effizienz zu vereinen, ohne dabei den Fokus auf die Interessen des Kunden zu verlieren. Alles muss unter einen Hut gebracht werden. Daher müssen Unternehmen zwingend die Qualität, Kosten, Zeit und Nachhaltigkeit in der Produktion berücksichtigen, um langfristig erfolgreich zu bleiben. Denn Nachhaltigkeit bedeutet nicht nur, die Ressourcen zu sparen, sondern das Maximale aus einem Prozess heraus zu holen. Dies bedeutet folglich, dass Ressourcen in Form von Maschinen, Zeit, Energie und Rohstoffen gespart werden. Und gerade das nehmen sich viele Produzenten vor: Nachhaltigkeit und Kundenzufriedenheit zu kombinieren.
KSS-Verbrauch reduzieren? Grindaix macht es möglich.
Grindaix will genau die Unternehmen unterstützen, die zukünftig ihren ökologischen Fußabdruck reduzieren wollen. Speziell für einen sicheren und qualitativ hochwertigen Schleifprozess werden in der Industrie häufig sehr hohe KSS-Mengen mit hohen Austrittsgeschwindigkeiten und Drücken verwendet.
Der Anwender priorisiert eher zu viel KSS als zu wenig. Ein Bauteil mit einer Randzonenschädigung aufgrund von thermischer Überbelastung ist als Ausschuss anzusehen. Die für den hohen Druck notwendige Pumpen- und Filtertechnik ist nicht nur teuer, es wird ebenso ein hoher Energieaufwand benötigt.
Durch eine angepasste KSS-Düsentechnik können Kühlschmierstoffmengen und Energiebedarfe deutlich reduziert werden. Eine bedarfsgerechte Regelung der Zuführung durch Sensor- und Maschinensignale trägt ebenso dazu bei, dass die jeweiligen Mengen und Drücke nur zur benötigten Zeit aufgebracht werden.
Dazu werden vermehrt umweltverträgliche Öle mit einem niedrigen CO2-Fußabdruck entwickelt, welche einen weiteren Beitrag
hinsichtlich der Umweltentlastung leisten.
Bereits seit einigen Jahren konnte Grindaix mit den ersten prozessangepassten KSS-Düsen eine enorme Einsparung an Ressourcen bei den Kunden erreichen. Dieser Erfolg hat gerade in Zeiten der Energiekrise an Relevanz dazugewonnen. Bei unseren Kunden erreichen wir durch den Einsatz von optimierten und prozessangepassten Kühlschmierstoffdüsen eine KSS-Verbrauchsreduzierung von über 60%.
Das Ergebnis spricht deutlich für den Erfolg in der Ressourceneinsparung.
Durch die Identifikation der anlagenspezifischen Betriebsmittelzustände und der Optimierung der KSS-Zufuhr können Sie als Unternehmen etwas zu einer nachhaltigen Produktion beitragen. Der gezielte Einsatz von KSS (Kühlschmierstoffen) kann die Maß- und Formgenauigkeit, Oberflächengüte und Randzoneneigenschafte positiv beeinflussen. Durch die aufkommenden Vorschriften von Seiten der Regierung geraten immer mehr die bedarfsangepassten
und die prozessoptimierte Verwendung von Düsen in den Fokus der Unternehmen. Auch andere Faktoren verstärken den Fokus auf die Verwendung von KSS. Neben den technischen Leistungsfähigkeiten spielen auch wirtschaftliche, ökologische, sicherheits- und gesundheitsrelevante Aspekte eine entscheidende Rolle.
Anwendungsfall – Automobilzulieferer
In einem Fallbeispiel wurde eine Fertigungseinheit mit 54 Werkzeugmaschinen optimiert. Der Verbrauch an Kühlschmierstoff konnte um 38% reduziert werden, ohne dass es dabei zu einer Produktivitäts- oder Qualitätseinbuße kam. Dies führte in der Folge dazu, dass u.a. 30% der elektrischen KSS-Kühlleistung eingespart werden konnte. Die KSS-Filtration wurde darüber hinaus deutlich im Durchsatz entlastet. Die KSS-Reinheit stieg an. Verschleißbedingte Maschinenausfälle nahmen messbar ab.
Insgesamt wurden 285.000€ an KSS bezogene Kosten jährlich (bereits im ersten Betriebsjahr) eingespart. Die Investition in Optimierungsmaßnahmen betrug 136.000€, sodass der Return on Investment nach nur sechs Monaten erreicht wurde.
Sie sind interessiert an einem Gespräch und wollen auch mit Ihrer Maschine ressourcenschonend produzieren?
Schauen Sie einmal bei uns im Katalog vorbei oder stellen Sie uns eine Anfrage auf info@grindaix.de.
Wir freuen uns darauf, von Ihnen zu hören.
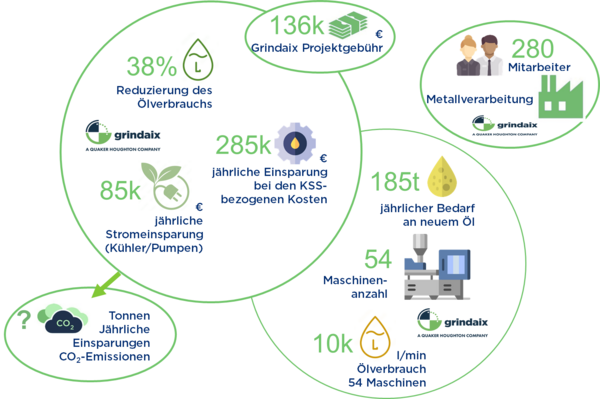
In diesem Artikel relevante Produkte:
Diese Artikel aus unserem Magazin könnten Sie auch interessieren:
KSS-Versorgung
Das Schleifprozesse mit KSS versorgt werden müssen, ist leicht nachvollziehbar. Doch welche Aufgaben übernimmt der Kühlschmierstoff eigentlich genau und worin liegen die Herausforderungen bei der Kühlschmierstoffversorgung?
Ganzheitliche Prozessauslegung und -optimierung
Der Wandel in der Automobilindustrie und die angestrebte Reduktion von CO2-Emissionen, z. B. in der Luftfahrt, stellen die Schleiftechnik vor neue Herausforderungen. Die Zerspanung dünnwandiger Leichtbauteile sowie die Bearbeitung hochwarmfester Werkstoffe gewinnen an Bedeutung.