Zero Emission Production
This article deals with ZERO EMISSION PRODUCTION by digitizing existing machines (retrofit kit). It presents a technology package (hardware + software) based on artificial intelligence that supports manufacturing companies in sustainably reducing carbon dioxide emissions while increasing both the availability and productivity of production equipment and avoiding waste in the use of operating materials (compressed air, oil, water, electric power). In the medium term, this will enable savings in the payment of CO2 tax.
Why is it important to address the issue of zero-emissions production?
With regard to the importance of zero-emission production in the future, the data in the following figure show very clearly that the carbon dioxide content in the atmosphere, based on the recorded values of the last 800,000 years, has increased drastically and uncontrollably, especially in recent years. Carbon dioxide is one of the most important greenhouse gases and contributes significantly to global warming, which in turn leads to rising sea levels, stronger and more frequent weather extremes (heat and cold), worldwide drinking water shortages and many other undesirable effects. But it is not only the environment that is massively burdened by this, but also its society and the economy.
However, we want to be optimistic, as technological progress, in areas of digitalization technology and thus also artificial intelligence, allows us to develop predictive models in the form of software-based assistance systems and thus realize emission-free production in the long term.
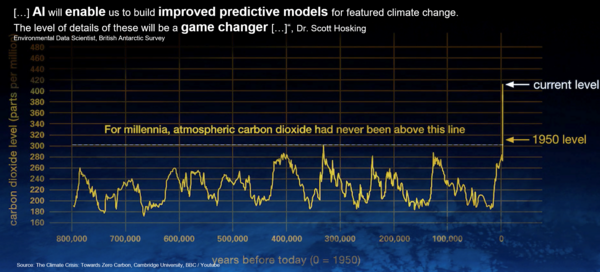
What challenges will manufacturing companies have to face in the future in the context of ZERO EMISSION PRODUCTION?

The requirements for companies have changed, as they now not only have to make a trade-off between quality, cost and time, but also have to consider sustainability in order to be successful in the long term. Up to now, the operating materials of the production equipment, which in total account for up to 16% of the resources consumed annually in manufacturing companies, have not been continuously provided according to demand.
On the contrary, 80% of the companies do not know the plant-specific operating resource conditions and their consumption related to the individual production machines. This dilemma leads to a concrete need to measure the consumption of operating materials, because what is not known cannot be improved.
The diagram shows examples of typical values for the energy consumption of a machine tool. In particular, the reduction of cooling lubricant consumption offers a high potential for improving the energy balance, as it accounts for almost 60% of the total energy demand. To reduce emissions as quickly as possible and ensure more sustainable production, plant efficiency must be increased. This can be made possible with the help of analysis systems that provide users in manufacturing companies with concrete recommendations for action to avoid wasting operating materials. If the operating materials are supplied to the means of production in a constant quality and quantity as required at any time with regard to their physical and chemical states, this leads to a considerable savings effect in the consumption of resources in production companies.
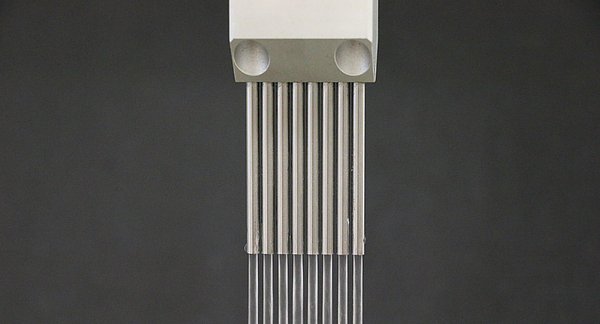
What is the concrete possibility of achieving the goal of avoiding waste of operating materials?
If we look at the roadmap for digitizing inventory machines on the way to reducing the carbon footprint of, for example, metalworking machine tools, we see the following:
In a first step, we consider metalworking machine tools that require operating materials to function properly. Due to the mostly missing sensor technology for the most exact recording of the operating material consumption, this information is not available to the operator of the production equipment. Nor is the cycle-related requirement for operating materials per component known. Although the machine controls valves (open/close), this is usually not related in a concretely quantified way to a measurand such as liters per minute (l/min). Therefore, the CO2 footprint of the produced component is not known. Rather, it is estimated quite superficially, based on total consumption and total quantities. The technical condition of the respective equipment supply is also not known. Any malfunctions are therefore only reactively and manually eliminated by the machine operators, but not preemptively avoided or remedied during planned downtimes (maintenance shifts).
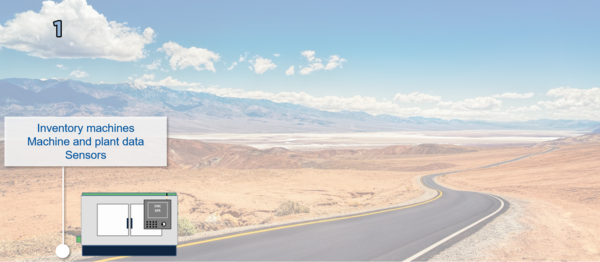
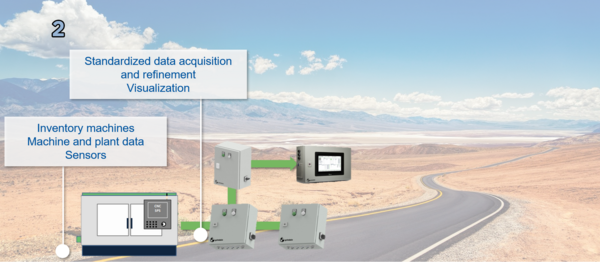
In order for this to succeed in the future, a corresponding infrastructure of digitization technology is necessary. The requirements for proper digitization of existing machines are:
- Reliable data acquisition, high data quality through suitable sensor technology
- reasonable sampling rates and secure data storage
- Visualization of the measured variables in the production area
- A softwarebased monitoring of the operating material data
- Provision of the data in OPCUA format to further IT
These requirements must first be met in order to enable the subsequent meaningful integration of artificial intelligence. With modern machine learning methods, artificial intelligence can be trained in such a way that it can meaningfully develop a practical potential for data-driven analyses and correlation finding.Only in the next step do we start with a software-based identification and recognition of the normal states of the process flows. This is necessary to be able to detect various deviations from the normal state. This is followed by the classification and interpretation of operating material states, consumptions and deviations through data-driven analysis. At the same time, production-specific key figures (component-related consumption indicators) are formed from this information, which for the first time allow concrete statements to be made on production-cycle-specific operating material consumption.
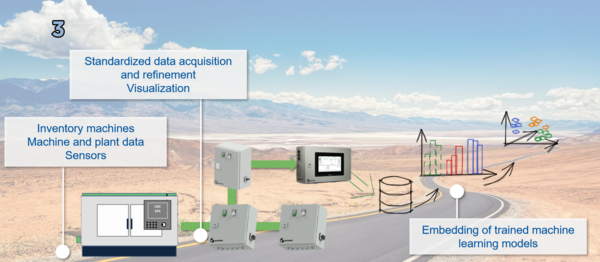
![[Translate to Englisch:] Grindaix-digital-assistant-4 [Translate to Englisch:] Grindaix-digital-assistant-4](https://grindaix.de/fileadmin/_processed_/c/5/csm_Grindaix-digital-assistant-4_12fc05b3e7.png)
Using information feedback, the software succeeds in checking and continuously improving the effectiveness of its recommendations for action. Ultimately, the digital assistant provides the user with concrete and maximum value-added decision-making aids for the operation of production equipment for machine operators, but also for the optimization of production equipment for engineering, maintenance and production planning departments.
If all these steps work in harmony, then predictive maintenance as well as resource consumption-oriented process optimization will achieve the goal of a sustainable reduction in CO2 emissions while simultaneously increasing the economic efficiency of production processes.
What does this digital assistant for reducing CO2 consumption in productions look like?
The digital assistant is a software that also runs your computer. The software works in three steps.
First, the data is evaluated statistically. The result is an indication of the current consumption data and component-related performance indicators such as CO2 emission per component. This current data is then compared to historical data to determine how you are doing in terms of operating material consumption - example: "You have consumed 8.7% more operating materials this week than the average of the 62 calendar weeks before!" All machine tool process consumptions are defined by their CO2 equivalent. At this point, the evaluation of the actual condition already represents a significant added value for most customers.
The second stage involves the application of rule-based methods (if then causalities) for IDentification, analysis and learning of correlations. Example: pressure upstream of line 2 constant - pressure downstream of line 2 decreases steadily àline 2 becomes increasingly clogged!".
In the third stage, decision support is presented by applying non-rule-based methods. For example, the purely data-driven, unsupervised learning methods: The previously unknown newly recognized correlations are revealed and recommended actions are generated. Example: " Whenever we produce scrap on machine 3, machines 4,5,6 and 7 run simultaneously at maximum operating material consumption. Operating material supply for machine 3 reduced!"
![[Translate to Englisch:] Grindaix-Stages-1-3 [Translate to Englisch:] Grindaix-Stages-1-3](https://grindaix.de/fileadmin/_processed_/5/c/csm_Grindaix-Stages-1-3_16be7b70ca.png)
Let's look at the graphical user interface of the operating fluid monitoring system. The special feature of the user interface is that it can be accessed at any time and from anywhere, i.e. device-independent, via a secure web browser.
![[Translate to Englisch:] Grindaix-System-1 [Translate to Englisch:] Grindaix-System-1](https://grindaix.de/fileadmin/_processed_/6/5/csm_Grindaix-System-1_3fda6a1719.png)
![[Translate to Englisch:] Grindaix-system-2 [Translate to Englisch:] Grindaix-system-2](https://grindaix.de/fileadmin/_processed_/b/7/csm_Grindaix-system-2_805e9e294d.png)
The monitoring function answers your questions about when (e.g. every second), how much (quantity), in which condition (e.g. pressure, temperature, chemical consistency, pH value, ...) and at which point (machine no. 3, line 4, consumer 5) operating resources are consumed. Deeper insights can be generated by viewing the analysis interface. This function can be used to retrieve correlations that are not obvious at first glance. For example, a cluster analysis is displayed here for the condition of the operating material feed technology and the carbon dioxide emissions per process cycle of the component production and also production downtime. With this system, savings opportunities can be identified quickly and clearly and the monitoring of sustainability targets can be realized much more easily.
For which machines is this system suitable? Can it be used for all types of machines?
The digital assistant for reducing the consumption of operating materials in production companies is possible for all machine types and machine generations. The machines are subdivided according to feed and age.
The figure shows 3 categories (type 1 to 3) for different stock machines:
Type 1 is the oldest type of machine tool. It can be up to 15 years old. We completely retrofit these types of machines, including sensor installation and networking. For this type of inventory machine, successful digitization and connection to the Grindaix Monitoring System takes about 16 weeks.
The second type of machines (type 2) are middle-aged machines. They can be between 3 and 15 years old. These machines may already have some fluid sensors, but are not fully professionally equipped and not digitally networked. They can be properly digitized and integrated into the grindaix infrastructure within eight weeks.
The third type is a maximum of three years old. These new machines have operating material monitoring technology that meets requirements and output operating material data in OPC UA format. This machine tool can be integrated into the grindaix infrastructure within just two weeks.
![[Translate to Englisch:] Grindaix-types_4 [Translate to Englisch:] Grindaix-types_4](https://grindaix.de/fileadmin/_processed_/2/f/csm_Grindaix-types_b628cc02e1.png)
Regardless of the type of machine, the sensor technology installed or yet to be installed, and the IT infrastructure, it is possible to digitize machines and plants. This is the necessary prerequisite for the use of artificial intelligence
Products relevant to this article:
You may also be interested in these articles from our magazine:
Filtration in the cooling lubricant circuit
The cooling lubricant filtration unit is an important and central component of the cooling lubricant circuit. In this magazine article, you can find out what it is and which components are important.
Resource-saving cooling lubricant supply
Government regulations mean that companies are placing more emphasis on their ecological footprint. So is it possible to save resources and optimize production at the same time? Find out more about how this is possible here.
Energy savings during grinding
In times of energy crisis, companies must act. Are there ways to save energy when grinding? We present a few possibilities.