Zero Emission Production
Dieser Artikel befasst sich mit der ZERO EMISSION PRODUCTION durch Digitalisierung von Bestandsmaschinen (Nachrüstsatz). Dabei wird ein auf künstlicher Intelligenz basierendes Technologiepaket (Hardware + Software) vorgestellt, das produzierende Unternehmen dabei unterstützt, Kohlendioxidemissionen nachhaltig zu reduzieren und gleichzeitig sowohl die Verfügbarkeit als auch die Produktivität der Produktionsmittel erhöht sowie Verschwendungen im Gebrauch von Betriebsstoffen (Druckluft, Öl, Wasser, elektrischer Strom) vermeidet. Mittelfristig werden dadurch Einsparungen bei der Zahlung der CO2-Besteuerung möglich.
Warum ist es wichtig, sich mit dem Problem der emissionsfreien Produktion zu befassen?
In Bezug auf die Bedeutung einer zukünftig emissionsfreien Produktion zeigen die Daten im folgenden Bild sehr deutlich, dass der Kohlendioxidgehalt in der Atmosphäre anhand der aufgezeichneten Werte der letzten 800.000 Jahre vor allem in den letzten Jahren drastisch und unkontrolliert gestiegen ist. Kohlendioxid ist eines der wichtigsten Treibhausgase und trägt erheblich zur globalen Erwärmung bei, was wiederum zu einem Anstieg des Meeresspiegels, stärkeren und häufigeren Wetterextremen (Hitze und Kälte), weltweiter Trinkwasserknappheit und vielen anderen unerwünschten Auswirkungen führt. Aber nicht nur die Umwelt wird dadurch massiv belastet, sondern auch deren Gesellschaft und die Wirtschaft.
Wir wollen jedoch optimistisch sein, da es uns der technologische Fortschritt, in Bereichen der Digitalisierungstechnik und damit auch der künstlichen Intelligenz, erlaubt Vorhersagemodelle in Form von softwarebasierten Assistenzsystemen zu entwickeln und dadurch langfristig eine emissionsfreie Produktion zu realisieren.
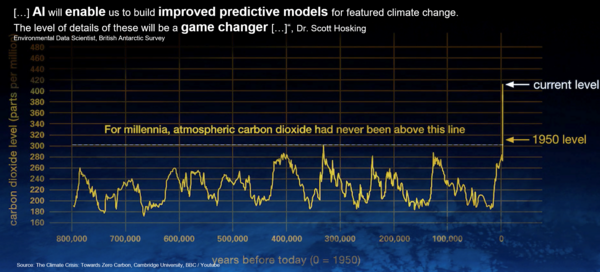
Welchen Herausforderungen müssen sich produzierende Unternehmen im Kontext einer ZERO EMISSION PRODUCTION zukünftig stellen?

Die Anforderungen an Unternehmen haben sich geändert, da sie nun nicht nur einen Kompromiss zwischen Qualität, Kosten und Zeit eingehen müssen, sondern auch die Nachhaltigkeit berücksichtigen müssen, um langfristig erfolgreich zu sein.
Bisher wurden die Betriebsstoffe der Produktionsmittel, die in Summe bis zu 16% der jährlich verbrauchten Ressourcen in produzierenden Unternehmen ausmachen, nicht kontinuierlich bedarfsorientiert bereitgestellt.
Vielmehr kennen 80% der Unternehmen die anlagenspezifischen Betriebsmittelzustände und deren auf die einzelnen Produktionsmaschinen bezogenen Verbräuche nicht. Dieses Dilemma führt zu einem konkreten Bedarf die Betriebsstoffverbräuche zu messen, denn was man nicht kennt kann man auch nicht verbessern.
Das Diagramm zeigt exemplarisch typische Werte für den Energieverbrauch einer Werkzeugmaschine. Insbesondere die Reduzierung des Kühlschmierstoffverbrauchs bietet ein hohes Potenzial zur Verbesserung der Energiebilanz, da sie fast 60% des gesamten Energiebedarfs ausmacht. Um die Emissionen so schnell wie möglich zu reduzieren und eine nachhaltigere Produktion zu gewährleisten, muss die Anlageneffizienz gesteigert werden. Dies kann mithilfe von Analysesystemen ermöglicht werden, die dem Anwender in produzierenden Unternehmen konkrete Handlungsempfehlungen zur Vermeidung von Betriebsstoffverschwendungen geben.
Werden die Betriebsstoffe hinsichtlich Ihrer physikalischen und chemischen Zustände in konstanter Qualität, bedarfsgerechter Menge zu jeder Zeit anforderungsgerecht den Produktionsmittel zugeführt, so führt dies zu einem in Summer erheblichen Einsparungseffekt beim Ressourcenverbrauch in Produktionsunternehmen.
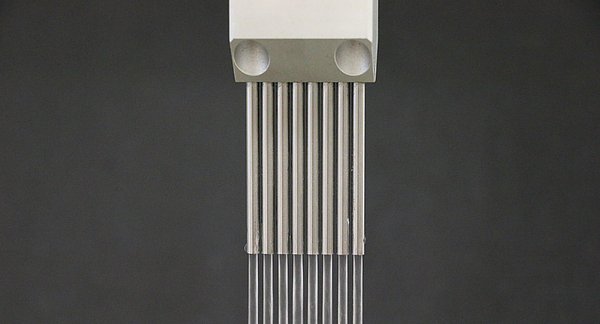
Welche Möglichkeit besteht denn, das Ziel der Vermeidung von Betriebsstoffverschwendungen konkret zu erreichen?
Wenn wir uns die Roadmap für die Digitalisierung von Bestandsmaschinen auf dem Weg zur Reduzierung des CO2-Footprints von beispielsweise metallverarbeitenden Werkzeugmaschinen ansehen, erkennen wir Folgendes:
In einem ersten Schritt betrachten wir metallverarbeitende Werkzeugmaschinen, die Betriebsstoffe benötigen, um sachgerecht zu funktionieren. Aufgrund der meist fehlenden Sensorik zur möglichst exakten Erfassung der Betriebsmittelverbräuche, stehen diese Informationen dem Betreiber der Produktionsmittel nicht zur Verfügung. Ebenso wenig bekannt ist der zyklusbezogene Bedarf an Betriebsstoffen je Bauteil. Die Maschine steuert zwar Ventile (auf/zu), doch meist steht dies nicht in einem konkret quantifizierten Zusammenhang mit einer Messgröße wie beispielsweise Liter pro Minute (l/min). Daher ist der CO2-Footprint des produzierten Bauteils nicht bekannt. Er wird vielmehr recht oberflächlich, anhand der Gesamtverbräuche und Gesamtstückzahlen, abgeschätzt. Auch nicht bekannt ist der technische Zustand der jeweiligen Betriebsmittelversorgung. Etwaige Störungen werden daher von den Betreibern der Maschinen nur reaktiv und manuell beseitigt, nicht jedoch vorausschauend vermieden oder in geplanten Stillstandzeiten (Wartungsschichten) behoben.
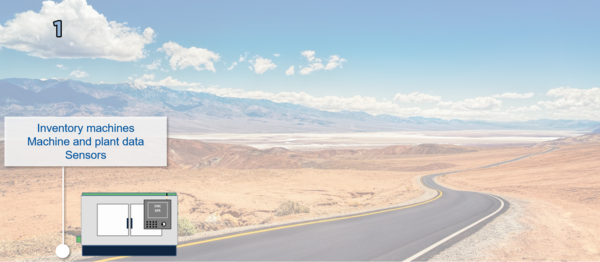
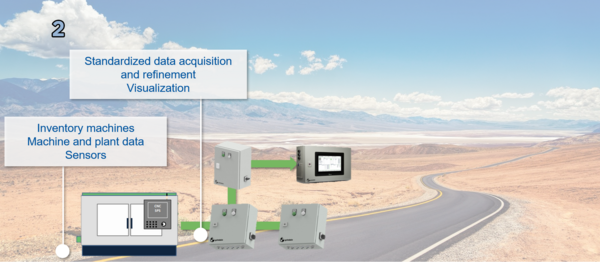
Damit dies zukünftig gelingt ist eine entsprechende Infrastruktur einer Digitalisierungstechnik nötig. Anforderungen an eine sachgerechte Digitalisierung von Bestandsmaschinen lauten:
- zuverlässige Datenerfassung, hohe Datenqualität durch geeignete Sensorik
- sinnvolle Abtastraten und sichere Datenspeicherung
- Visualisierung der Messgrößen im Produktionsbereich
- Eine softwarebasierte Überwachung der Betriebsstoffdaten
- Bereitstellung der Daten im OPC-UA Format an weiterführende IT
Diese Anforderungen müssen zunächst erfüllt werden um eine nachfolgend sinnvolle Integration der Künstlichen Intelligenz zu ermöglichen. Mit modernen Methoden des maschinellen Lernens kann man eine künstliche Intelligenz dergestalt trainieren, dass sie ein praxisgerechtes Potenzial für datengesteuerte Analysen und Korrelationsfindung sinnvoll entfalten kann.
Erst im nächsten Schritt beginnen wir mit einer softwarebasierten Identifizierung und Erkennung der normalen Zustände der Prozessabläufe. Dies ist notwendig, um verschiedene Abweichungen vom Normalzustand erkennen zu können. Darauf folgt die Klassifizierung und Interpretation von Betriebsstoff-Zuständen, -Verbräuchen und Abweichungen durch datengesteuerte Analyse. Zeitgleich werden aus diesen Informationen produktionsindividuelle Kennzahlen (bauteilbezogene Verbrauchs-Indikatoren) gebildet die erstmals konkrete Aussagen zu produktionszyklusindividuellen Betriebsstoffverbräuchen erlauben.
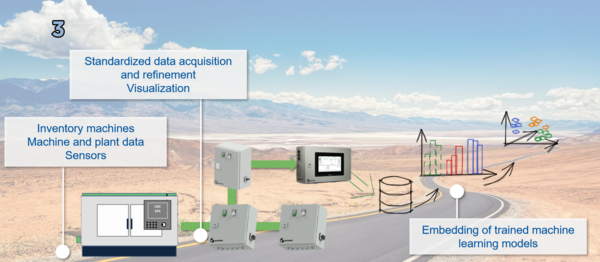
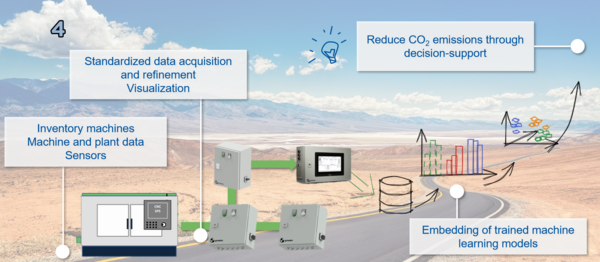
Unter Nutzung von Informationsrückkopplungen gelingt es der Software die Wirksamkeit seiner Handlungsempfehlungen zu prüfen und stetig zu verbessern. Letztendlich bietet der digitale Assistent dem Anwender konkrete und maximal wertschöpfende Entscheidungshilfen zum Betrieb der Produktionsmittel für Maschinenbediener, aber zur Optimierung der Produktionsmittel für Engineering, Instandhaltung und Fertigungsplanungsabteilungen.
Arbeiten alle diese Schritte im Einklang, dann wird durch eine vorausschauende Instandhaltung sowie eine ressourcenverbrauchsorientierte Prozessoptimierung das Ziel einer nachhaltigen Reduktion der CO2-Emissionen bei gleichzeitiger Erhöhung der Wirtschaftlichkeit der Produktionsprozesse erreicht.
Wie sieht dieser digitale Assistent zur Reduktion des CO2-Verbrauchs in Produktionen aus?
Der digitale Assistent ist eine Software die auch Ihrem Computer betrieben wird. Die Software arbeitet in drei Schritten.
1. Zunächst werden die Daten statistisch ausgewertet. Es entsteht eine Angabe der aktuellen Verbrauchsdaten und bauteilbezogenen Leistungsindikatoren wie CO2-Emmision je Bauteil. Diese aktuellen Daten werden anschließend mit Historiendaten verglichen um festzustellen wie man sich in Bezug auf den Betriebsstoffverbrauch entwickelt – Beispiel: „Sie haben in dieser Woche 8,7% mehr Betriebsstoffe verbraucht als im Durchschnitt der 52 Kalenderwochen zuvor!“ Alle Prozessverbräuche der Werkzeugmaschinen werden über deren CO2-Äquivalent definiert. Zu diesem Zeitpunkt stellt die Bewertung des tatsächlichen Zustands für die meisten Kunden bereits einen erheblichen Mehrwert dar.
2. Die zweite Stufe beinhaltet die Anwendung von regelbasierten Methoden (Wenn dann Kausalitäten) zur Identifikation, Analyse und Erlernung von Zusammenhängen. Beispiel: Druck vor Leitung 2 konstant – Druck nach Leitung 2 sinkt stetig -> Leitung 2 verstopft zunehmend!“.
3. In der dritten Stufe wird die Entscheidungsunterstützung durch Anwendung nicht regelbasierter Methoden dargestellt. Zum Beispiel die rein datengesteuerten, nicht überwachten Lernmethoden: Die bis dahin unbekannten neu erkannten Zusammenhänge werden aufgedeckt und Handlungsempfehlungen generiert. Beispiel: „ Immer wenn wir an Maschine 3 Ausschuss produzieren, laufen Maschine 4, 5, 6 und 7 gleichzeitig bei maximalem Betriebsstoffverbrauch. Betriebsstoffzuführung für Maschine 3 reduziert!
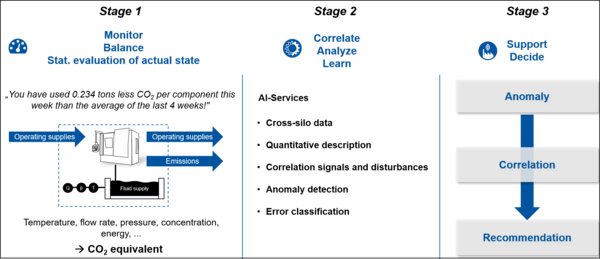
Betrachten wir die grafische Benutzeroberfläche des Betriebsstoff-Überwachungssystems. Das Besondere an der Benutzeroberfläche ist, dass sie jederzeit und überall, d.h. geräteunabhängig, über einen sicheren Webbrowser aufgerufen werden kann.
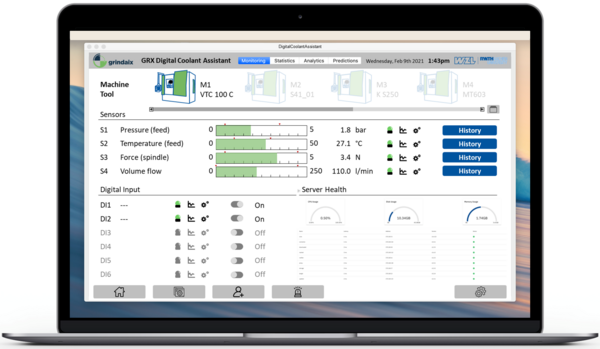
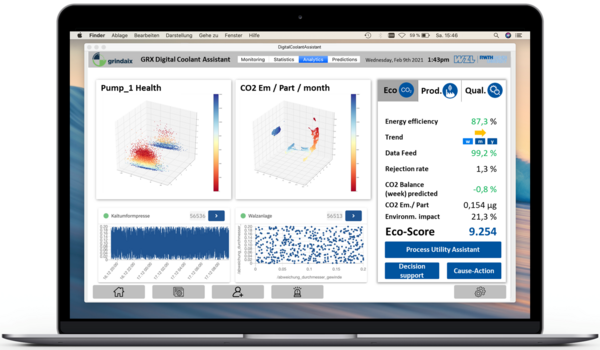
Die Überwachungsfunktion beantwortet Ihnen Fragen, wann (bspw. zu jeder Sekunde), wie viel (Mengenangabe) in welchem Zustand (bspw. Druck, Temperatur, chemische Konsistenz, pH-Wert, …) und an welcher Stelle (Maschine Nr. 3, Leitung 4, Verbraucher 5) Betriebsressourcen verbraucht werden. Tiefere Einblicke können durch Betrachten der Analyseschnittstelle generiert werden. Mit dieser Funktion können Korrelationen abgerufen werden, die auf den ersten Blick nicht offensichtlich sind. Hier wird beispielsweise eine Clusteranalyse für den Zustand der Betriebsstoffzuführungstechnik und die Kohlendioxidemissionen je Prozesszyklus der Bauteilfertigung und auch Produktionsnebenzeit angezeigt. Mit diesem System können Einsparungsmöglichkeiten rasch und übersichtlich identifiziert und die Überwachung von Nachhaltigkeitszielen deutlich leichter realisiert werden.
Für welche Maschinen ist dieses System geeignet? Kann es für alle Arten von Maschinen verwendet werden?
Der digitale Assistent zur Reduktion der Betriebsstoffverbäuche in Produktionsunternehmen ist für grundsätzlich alle Maschinentypen und Maschinengenerationen möglich. Man unterteilt dabei die Maschinen nach Zustand und Alter.
In der Abbldung sind 3 Kategorien (Typ 1 bis 3) für verschiedene Bestandsmaschinen dargestellt:Typ 1 ist der älteste Werkzeugmaschinentyp. Es kann bis zu 15 Jahre alt sein. Wir rüsten derartige Maschinen vollständig um, einschließlich Sensorinstallation und Vernetzung. Für diesen Typ von Inventarmaschine dauert die erfolgreiche Digitalisierung und Anbindung an das Grindaix Monitoring System etwa 16 Wochen.
Der zweite Maschinentyp (Typ 2) sind Maschinen mittleren Alters. Sie können zwischen 3 und 15 Jahre alt sein. Diese Maschinen verfügen möglicherweise bereits über einige Flüssigkeitssensoren, sind jedoch nicht vollständig fachgerecht ausgerüstet und nicht digital vernetzt. Sie können innerhalb von acht Wochen sachgerecht digitalisiert und in die grindaix-Infrastruktur integriert werden.
Der dritte Typ ist maximal drei Jahre alt. Diese neuen Maschinen besitzen anforderungsgerechte Betriebsstoffüberwachungstechnik und geben Betriebsstoffdaten im OPC UA-Format aus. Diese Werkzeugmaschine kann innerhalb von nur zwei Wochen in die grindaix-Infrastruktur integriert werden.
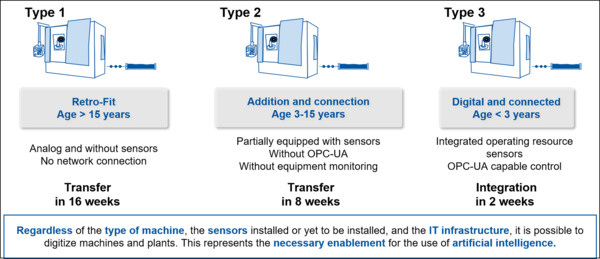
Unabhängig vom Maschinentyp, der installierten oder noch zu installierenden Sensortechnologie und der IT-Infrastruktur ist es möglich, Maschinen und Anlagen zu digitalisieren. Dies ist die notwendige Voraussetzung für den Einsatz künstlicher Intelligenz.
In diesem Artikel relevante Produkte:
Diese Artikel aus unserem Magazin könnten Sie auch interessieren:
KSS-Filtrationsanlagen
Die Aufbereitung ist ein entscheidender Teil der Kühlschmierstoffversorgung mit großen Einfluss auf das Fertigungsergebis und die Effizienz. Wir haben die üblichen Filtrationsverfahren für KSS beschrieben und gegenübergestellt.
Ressourcensparende KSS-Zufuhr
Bestimmung von Seiten der Regierung sorgen dafür, dass Unternehmen
mehr Wert auf ihren ökologischen Fußabdruck legen.
Kann also gleichzeitig Ressourcen gespart und die Produktion
optimiert werden? Hier erfahren Sie mehr darüber wie dies möglich ist.
Energieeinsparungen beim Schleifen
In Zeiten der Energiekrise müssen Unternehmen handeln. Gibt es Möglichkeiten beim Schleifen Energie zu sparen? Wir stellen Ihnen ein paar Möglichkeiten vor.