KI - Umsetzung
Im Folgenden wird an einem Beispiel demonstriert, wie man ein Digitalisierungsprojekt erfolgreich umsetzen kann.
Auditierung des Produktionssystems: In einem ersten Schritt werden in einem Kundengespräch vom Anwender die jeweiligen zu überwachenden Produktions-Komponenten (Was soll überwacht werden?) und die erwarteten Überwachungsergebnisse (Welche Aussage des Produktions-Überwachungssystems wird in welcher Form und welchen Ausgabedatenformaten, erwartet?) formuliert.
Im zweiten Schritt analysiert die Grindaix GmbH beim Kunden vor Ort die Umsetzbarkeit der Kundenanforderungen über die logische Verknüpfung verschiedener möglicher Sensorsignale an verschiedenen Einsatzstellen (Zugänglichkeit, Einbringung, Signalschnittstellen, …) innerhalb des KSS-Systems.
Gerade die Signalschnittstellen sind sehr sorgfältig zu wählen. Hierbei führt die Grindaix GmbH ein detailliertes Coolant Audit-E (Elektronik) durch, in dem die Schnittstellen aller avisierten KSS-Systemkomponenten auf Eignung analysiert werden und liefert genau dort konkrete Umbauempfehlungen (Stromlaufplan, Stückliste, Hardware, Software) wo die Schnittstellen für den Anschluss eines KSS-Monitoring Systems noch nicht anforderungsgerecht ausgelegt sind.
Anschließend werden die notwendigen Schnittstellen im Produktion-System des Kunden hergestellt bzw. genutzt. Die Sensoren werden in das Produktions-System integriert, verkabelt und mit einer übergeordneten Leitstelle (Condition Monitoring Pad) verknüpft.
Das Condition Monitoring Pad ist die Leitstelle des Produktions-Überwachungssystems und dient der zentralen Aufzeichnung aller verbauten Sensorsignale. Softwareseitig werden hier obere und untere Grenzwerte definiert, ab wann ein Sensorsignalwert als Fehler identifiziert werden kann. Daraufhin werden sogenannte Plausibilitätsszenarien programmiert, welche aufgrund des logischen Zusammenhanges verschiedenster Produktions-Sensorsignale Aussagen formulieren, die über die einzelne Zustandsüberwachung einer Produktions-Komponente hinausgehen (siehe beispielsweise zuvor beschrieben - Differenzdruckverlust in Rohrleitungen). Ferner werden die Abtastraten bestimmt, also wie oft man ein Sensorsignal messen und aufzeichnen (abspeichern) will, um ein späteres Produktion Data Tracking (GRX-PDT) zu ermöglichen.
Bei der Inbetriebnahme des Systems werden Testläufe durchgeführt, die den Produktionsbetrieb nicht beeinflussen (Status „lesen“!). Grenzwerte werden angepasst, Messreihen werden zu Testzwecken aufgezeichnet und analysiert. Es beginnt die Lern- (Teach-In) Phase des Produktions-Überwachungs-Systems. In einer folgenden Interaktionsphase können, je nach Kundenforderung, die Regelungsmechanismen sukzessive aktiviert werden um die adaptive Steuerung der Produktions-Komponenten zu ermöglichen. Ist dieser Prozess abgeschlossen, so kommt es zur Abnahme des Produktions-Überwachungssystems. Die Mitarbeiter werden in der Handhabung des Überwachungssystems geschult und in die Wartungsmöglichkeiten eingewiesen.
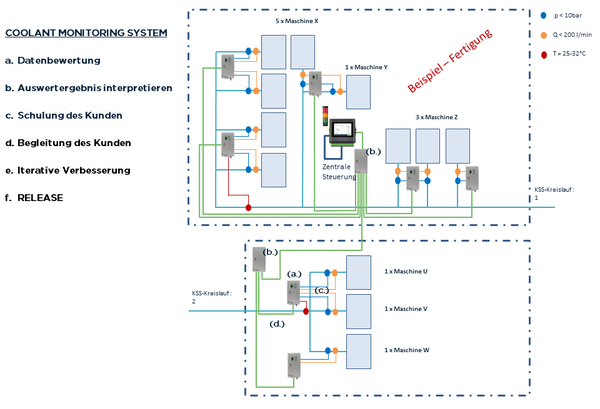
Es muss zu jeder Zeit vermieden werden, dass die hier beschriebene Sensorintegration das Produktionssystem zu anfällig für mögliche Messfehler macht. Daher kann das Überwachungssystem zunächst auch nur „lesend“ arbeiten und gibt Fehlermeldungen an eine übergeordnete Leistelle ab, ohne in den Produktionsablauf einzugreifen. Weiterführende Überwachungssysteme regeln gezielt verschiedenste Größen innerhalb der Produktionseinheit, um die kundenseitig gewünschte KSS-Versorgung zu jeder Zeit aufrecht zu erhalten.
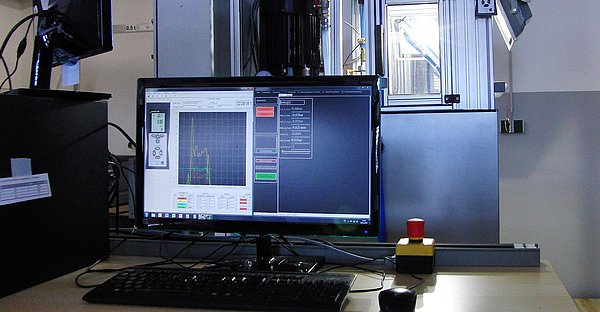
Schnittstellen zu Maschinen als Signal-Sollwert-Geber (bspw. Druckbedarfszyklen an frequenzgeregelten Pumpen) müssen fast grundsätzlich erstellt werden. Meist liegen diese nicht vor und der Systemlieferant erlaubt keinen Eingriff in seine Systemelektronik ohne Gewährleistungsabgabe. Daher müssen derartige Schnittstellen entweder über Profinet/-busschnittstellen (Bussysteme) oder anhand von Trennverstärkern zur Gewährleistung einer galvanischen Trennung der elektrischen Signale, entweder über geeignete Dienstleister oder über den Systemlieferanten selbst, zusätzlich erbracht werden.
Unter galvanischer Trennung oder Entkopplung versteht man das Vermeiden der elektrischen Leitung zwischen zwei Stromkreisen, zwischen denen Leistung oder Signale ausgetauscht werden sollen. Damit wird eine Beeinflussung des Stromkreislaufs des Signalgebers (Werkzeugmaschine, Filtrationsanlage, Pumpe, …) unterbunden.
Dieser zusätzliche Aufwand führt zu einem höheren Investitionsvolumen und stellt zunächst ein Hemmnis bei der Umsetzung einer digitalisierten Systemtechnik dar. Sind dabei jedoch die Vorteile kalkulierbar, so lässt sich ein konkreter Amortisationszeitraum bereits ohne die Nutzung einer künstlichen Intelligenz bestimmen.
In diesem Artikel relevante Produkte:
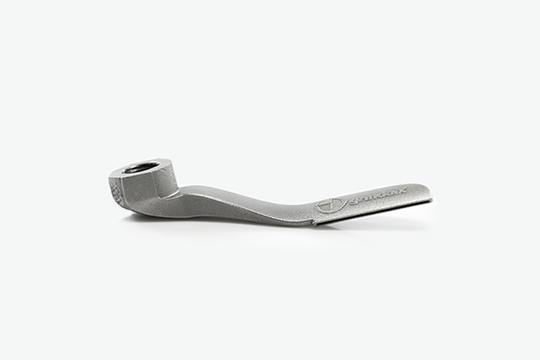
Diese Artikel aus unserem Magazin könnten Sie auch interessieren:
KSS-Filtrationsanlagen
Die Aufbereitung ist ein entscheidender Teil der Kühlschmierstoffversorgung mit großen Einfluss auf das Fertigungsergebis und die Effizienz. Wir haben die üblichen Filtrationsverfahren für KSS beschrieben und gegenübergestellt.
KI - Was ist das?
Im Grunde genommen ist der Begriff der künstlichen Intelligenz in diesem Zusammenhang fachlich falsch platziert. Künstliche Intelligenz beschreibt die akademischen Bestrebungen des Menschen das menschliche Gehirn und dessen Leistungen zu erforschen und mit Hilfe rechnergestützter Methoden abzubilden.
KI - Risiken
Neben den vielen guten Möglichkeiten und hohen Nutzenpotenzialen der künstlichen Intelligenz in der Produktionstechnik, bestehen ebenso Risiken, die es bei der Implementierung derartiger Fähigkeitswerkzeuge zu beachten gibt.